4″ Butterfly Valve: A Detailed Overview
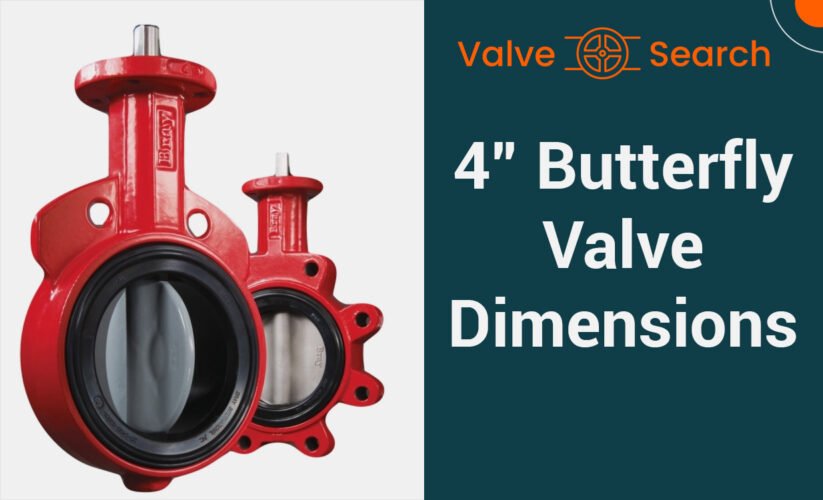
Introduction to 4″ Butterfly Valves
The world of fluid mechanics is filled with a plethora of valve types, each with its unique set of attributes that make it suitable for different applications. Among these is the 4″ Butterfly Valve, a component that plays a critical role in regulating the flow of liquids in various industries. This blog post aims to provide a comprehensive understanding of the 4″ Butterfly Valve, delving into its construction, materials, technical details, dimensions, and common applications.
Understanding What a 4″ Butterfly Valve Is
A 4″ Butterfly Valve, quite simply, is a valve that features a 4-inch diameter and operates using a straightforward mechanism. Its design, which incorporates a rotating disk in the center, bears a striking resemblance to a butterfly spreading its wings—thus the name. The disk rotation mechanism allows for the valve to either open or close, controlling the flow of fluid through the system. Notably, the 4″ in the name is not a random measurement. Instead, it indicates the nominal diameter of the pipe in which the valve will be integrated. The simplicity of its design, coupled with its operational efficiency, has elevated the 4″ Butterfly Valve as a go-to option for fluid flow control in various systems and operational contexts.
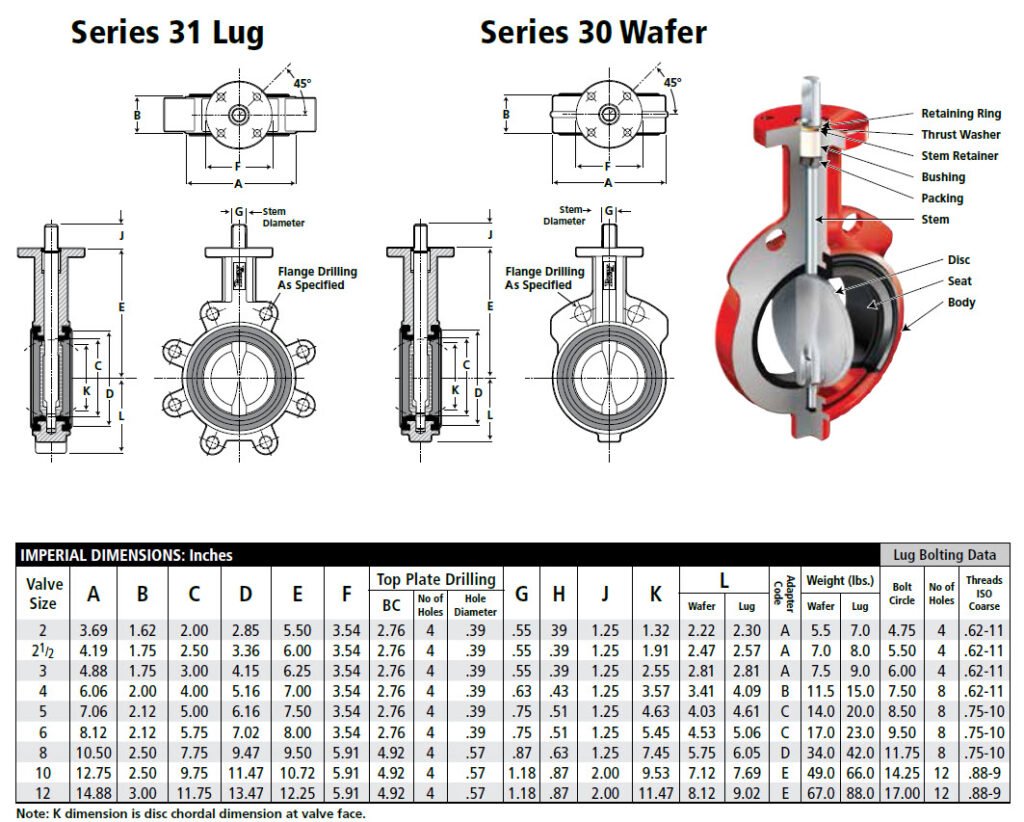
Butterfly Valve, Series 31
Construction and Materials of a 4″ Butterfly Valve
At the core of a 4″ Butterfly Valve lie four essential components: the body, disc, stem, and seat. The body forms a conduit for the fluid flow, with the disc at its heart, acting as the gatekeeper that controls the passage of fluid by rotating. The stem serves as the connecting link between the disc and the actuator, transmitting the rotational force from the actuator to the disc. Finally, the seat is the sealing interface that ensures there are no leaks when the valve is in the closed position.
The choice of material for these components heavily depends on the intended use of the valve. Certain common materials include cast iron, ductile iron, stainless steel, and PVC. Water and wastewater systems frequently opt for cast and ductile iron valves due to their durability and affordability. On the other hand, stainless steel valves are a popular choice for processes involving corrosive fluids, due to the material’s inherent corrosion resistance. For chemical processes that involve highly reactive substances, PVC offers an excellent choice due to its robust chemical resistance properties.
These materials do not only influence the valve’s performance and lifespan but also its compatibility with the fluid it will be regulating. Therefore, understanding the properties of these materials is essential in selecting the right 4″ Butterfly Valve for your system.
When deciding on the appropriate butterfly valve, it’s essential to remember that the valve’s materials need to withstand the system’s pressure and temperature conditions. It is also important to consider potential exposure to corrosive substances, UV radiation, and weather elements, especially for valves installed in outdoor or harsh environments.
Depending on the material used for construction, a properly installed and maintained 4 butterfly valve can have an expected service life of anywhere from five years to more than two decades before needing replacement or major repairs.
Key Technical Details to Consider
When it comes to choosing a 4″ Butterfly Valve, there are a number of critical technical specifics that must be kept in mind to ensure optimal performance and longevity. These specifics can largely be grouped into four categories: pressure rating, temperature rating, end connection type, and actuator type.
The pressure rating of a valve serves as an indicator of the maximum amount of pressure that the valve can safely handle. It is paramount to select a valve with a pressure rating that matches or exceeds the system’s maximum operating pressure to prevent failures or leaks.
The temperature rating, on the other hand, is the maximum temperature the valve can operate under without any loss in performance or structural integrity. This is particularly important for systems that deal with high-temperature fluids or are situated in environments with extreme temperatures.
The end connection type is another critical consideration. This term refers to how the 4″ Butterfly Valve will be connected to the pipe system. The three most common types are wafer, lug, and flanged connections. Wafer and lug connections are typically used in lighter applications where quick assembly and disassembly are needed, whereas flanged connections are often used in more permanent, high-pressure installations.
Lastly, the actuator type defines the method by which the valve is operated. The options typically include manual, pneumatic, electric, or hydraulic actuators. Manual actuators are the simplest and most cost-effective but require a human operator to manually open and close the valve. In contrast, pneumatic, electric, and hydraulic actuators allow for automated operation, providing greater precision and control, especially in complex systems with varying flow requirements.
While each of these details is crucial in its own right, it’s important to remember that they are interconnected. The choice of actuator type may influence the end connection type, and the system’s pressure and temperature conditions may dictate the valve’s required pressure and temperature ratings. Therefore, a comprehensive understanding of these technical details and how they interrelate is vital in selecting the ideal 4″ Butterfly Valve for your specific application.
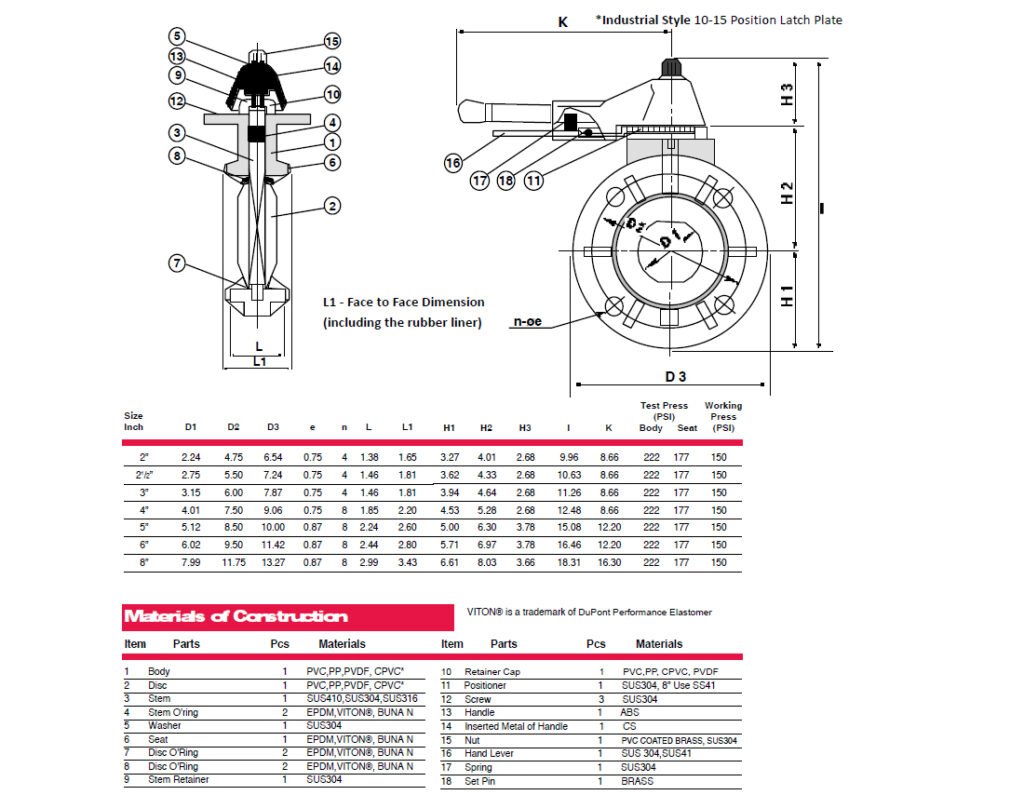
4″ Butterfly Valve Dimensions
Grasping the dimensions of a 4 inch butterfly valve is an integral part of ensuring its seamless operation and correct installation. These dimensions are not arbitrary but adhere to standard measures, facilitating proper integration into a pipeline system. Primarily, these dimensions consist of the face-to-face length, flange diameter, bolt circle diameter, number of bolt holes, and the diameter of the bolt holes.
Firstly, the face-to-face length refers to the linear measurement from one end of the valve to the other. This dimension is crucial in fitting the valve into the allotted space within the pipeline system. It’s worth noting that accurate measurement of the face-to-face length is vital to ensure the system’s overall efficiency and safety.
Next, the flange diameter is another key measurement. This refers to the outer diameter of the valve’s connecting end. This dimension plays a critical role in the connection between the valve and the pipe. A mismatch between the flange diameter of the valve and the pipeline can result in improper sealing, which can lead to leakage.
The bolt circle diameter represents the distance between the centers of the bolt holes. This measurement is integral in the alignment of the bolt holes during the valve installation process. Misalignment can lead to undue stress on the bolts, potentially causing premature failure.
Also, the number of bolt holes and the diameter of these holes are essential aspects. The bolt holes are used to secure the valve to the pipeline system. Therefore, their number and diameter must be compatible with the system’s bolting requirements to ensure a secure and leak-free connection.
Each of these dimensions plays a pivotal role in the correct installation and seamless operation of the 4″ Butterfly Valve. It is important to note that these dimensions must adhere to established standards. Non-standard measurements could result in incompatibility issues, potentially leading to improper sealing, leakage, or even failure of the system.
Common Applications of a 4″ Butterfly Valve
The 4″ Butterfly Valve is versatile and adaptable, finding its place in many industries due to its efficiency in controlling fluid flow. In the wastewater treatment sector, these valves play an essential role in controlling the flow of water and waste, contributing to the overall efficiency of the system.
The chemical industry also heavily relies on these valves. In situations where highly reactive or corrosive substances are involved, the chemical resistance properties of materials like PVC and stainless steel used in the 4″ Butterfly Valve become crucial. They help in maintaining the integrity of the system while ensuring smooth operation.
Food and beverage manufacturers also make use of these valves. They ensure a safe and efficient flow of various liquids during the production process. The design of the 4″ Butterfly Valve, particularly its easy-to-clean nature, is beneficial in maintaining the hygiene standards required in these industries.
In the HVAC industry, these valves contribute significantly to maintaining the desired environment in residential and commercial spaces. They regulate the flow of coolant or heating fluids, contributing to the overall temperature regulation of a space.
In fire protection systems, the 4″ Butterfly Valve’s critical role cannot be overstated. They are often used as control valves in sprinkler systems, regulating the flow of water when triggered by a fire alarm. This controlled flow ensures that sufficient water is dispersed to combat the fire while preventing water damage from excessive water flow.
Lastly, power generation facilities frequently use these valves to regulate the flow of steam or other fluids used in the generation process. This contributes to the overall efficiency of the power generation process while ensuring the safety of the system.
Conclusion for 4″ Butterfly Valves
In summary, the 4″ Butterfly Valve’s simplistic design, coupled with its efficient operation, makes it an indispensable component in various sectors. Whether it’s maintaining the efficiency of a wastewater system, ensuring the smooth operation in a chemical process, or keeping a residential building comfortably warm or cool, the 4″ Butterfly Valve’s versatility is evident in its numerous applications.