Comparing Globe Valves vs Ball Valves: A Guide to Their Distinct Advantages and Uses
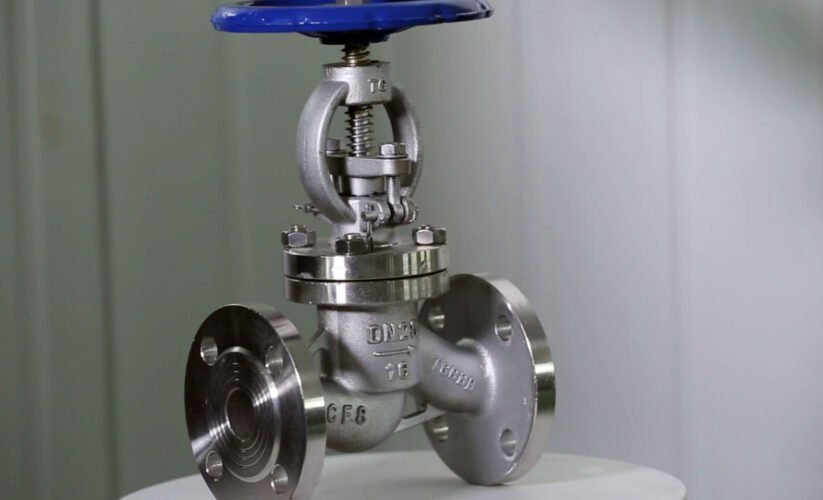
Table of Contents
ToggleWhat is the difference between a globe valve and a ball valve?
Understanding the differences in json between a globe valve and a ball valve is essential to making an informed decision for your particular application. In this blog post, we will compare the globe valve with the ball valve and consider its design, functionality, and best fit-for-use cases in your application.
Understanding Globe Valves
Globe valves are also the main components of different industrial uses since their design and functionality are versatile. The paper thus delves to discuss some basic aspect of the design of a globe valve, the operation of a globe valve, and some of its applications.
The Basics of Globe Valve Design
This is because of the somewhat spherical shape of their body when compared to other kinds of valves. It’s a linear actuated valve that comes in four main designs: straight flow, angle flow, cross flow, and oblique flow. Each design is tailored to specific operational requirements, such as pressure levels and flow characteristics.
The composition is very vital; ball disks, composition disks, and plug disks are used according to temperature, pressure, or the necessity for flow regulation.
How Does a Globe Valve Function?
Globe valves work through control of the flow of the fluid within a pipeline. Inside, it has a movable disk that can be regulated for fluid passage so that one can obtain the precise flow rate of the fluid. Turning the handwheel or actuator operates to either raise or lower the disk, thereby varying the flow passage and subsequently the flow rate. This makes, therefore, the globe valve useful where there is such a system that requires different and precise flow controls.
Common Applications of a Globe Valve
The application base for these globe valves is much wider, for applications such as power generation, oil and gas, water treatment, and chemical processing. These offer accurate control of flow and hence find the applications that need modulating flow, frequent operation, or throttling. On the flip side, globe valves find application in high-pressure and high-temperature system applications due to their ability to withstand the toughest operational conditions.
Understanding the basic design, function, and application of globe valves will ensure that these choices on selection and maintenance are adequately informed, thus ensuring efficient and safe processes in industries.
Exploring Ball Valves
The Structure of Ball Valves
Ball valves basically consist of a ball pivoted in a spherical outer shell, usually metallic, with a hole or port through which the fluid can go if the hole is in line with the valve openings.
This does, in fact, allow for tight sealing, as the ball rotates in order to block the flow. A very efficient one for many applications.
The Working Mechanism of Ball Valves
A ball valve works by rotating the ball inside the body of the valve either by a lever or a handle to control the flow of fluid. The ball then turns so that it blocks the passage, and the handle is perpendicular to the flow; then the flow stops. In case the handle is parallel to the flow, the fluid is then allowed to flow via the valve. This very simple, inexpensive, and effective mechanism makes it easy and fast for one to control the flow of fluids, be they liquids or gases.
Typical Uses for Ball Valves
Ball valves find very wide application in industries, home houses, or households due to their good reliability and ease of operation. They find wide applications when precision shut-off and regulation are demanded, from water and gas pipelines to petrochemical industries and even household plumbing systems. This makes it versatile and durable, available to the user across different sectors.
Key Differences Between Globe Valve and Ball Valve
Globe and Ball valves are very integral parts of the piping system in its totality. Each of them has very unique characteristics and service applications. The key major difference between both of these valves is key for decision making. The major differences are in the direction of flow, seal, and leakage; others include the consideration of pressure drop, maintenance, and durability.
Direction of Flow
In the context of flow direction, globe valves are designed to regulate the flow of fluid in a pipeline. They are designed with a moving disk and stationary ring for flow control with the highest accuracy. On the other side, the ball valves serve essentially in the application services of on/off, providing full stream when opened and fully shut when closed.
This basic difference in the capability to control the flow is the most important factor defining the two valves in the roles they play while operating in a system.
Seal and Leakage
Taking into consideration the property of sealing and leakages, globe valves have the sealing capacity properly defined due to the linear motion closing mechanism and hence very little, hence providing reliable shut-off. Ball valves, on the other hand, though excellent in sealing, might degrade the excellent seal because of the rotating ball element through time, maybe resulting in minimal leaks once closed.
Pressure Drop Considerations
Both varieties of valves have a different characteristic when it comes to the assessment of pressure drop: for globe valves, there is a relatively large pressure drop across the valve, and the act serves as a compromise for accurate flow control. In contrast, ball valves have a lower pressure drop due to their clear flow path upon complete opening of the valve, and thus, ball valves prove to be more advantageous when installed in application areas that require pressure loss to be kept to the minimum.
Maintenance and Durability
Globe valves are also known for their serviceability, which allows easy access to all parts for purposes of inspection and repairs. If the globe valves assure accessibility, it does not mean that they will be reliable in any use within an industrial setup.
Ball valves, on the other hand, even though they are very hardy and durable, might, from time to time, experience maintenance problems due to them having a complicated interior that might mean the kind of maintenance required is complicated.
Understanding this difference becomes very critical in selecting an appropriate valve type basing on several individual requirements of the system in concern and operational conditions. All these have specific advantages and limitations that are quite critically important within different industrial and commercial applications.
Advantages of using a Globe Valve
Precision in Flow Regulation
They give control of fluid flow in an accurate way. In some of the applications, this level cannot be spared. For instance, very accurate control flow will be required in just a few systems for them to run accordingly, and this will be the case with the majority of their applications. The other design with the world globe valve has a linear motion disk; this facilitates adjustment of flow and is appropriate for use in systems that call for fractional regulation.
A Globe Valve is Suitable for Throttling Applications
Globe valves are mainly considered suitable for throttling application requirements, where the part in which the valve has to be opened is at the part when affecting the regulation of flow. They are an ideal selection when fluid management is at a system that requires exact control because of their ability to work with varying amounts of flow and pressure differences. This versatility allows for reliable performance in diverse industrial and commercial settings.
Enhanced Sealing Capabilities
One of the key advantages of globe valves is their excellent sealing capabilities.
The design of the plug, with perpendicular motion to the flow, ensures that sealing is tight by forcing the plug downwards onto the seat, hence leaving reduced chances for any leak to occur. This is very critical for those systems to which failure by leakage might expose safety hazards or operational inefficiency. The enhanced sealing capabilities of globe valves contribute to their reliability in demanding applications.
Advantages of Ball Valves
Here are some of the advantages of the ball valve design in various industrial applications. The following are some of the major advantages of a ball valve:
Full Shut-off Capabilities
Great shut-off capability is offered by the ball valves, where the fluid undergoes no passing through the system if the valve is in the fully closed position. It contains a spherical closure element design that allows for sealing tightness and totally blocks the flow path.
This capability is also critical when, through control of fluid to absolute isolation, stopping any form of leakage and allowing system integrity is required.
Low Maintenance and High Durability
Ball valves are celebrated for their minimal maintenance requirements and outstanding durability, primarily due to their straightforward design featuring few moving parts. This simplicity significantly diminishes the frequency of required maintenance and servicing. The ball and seat components typically exhibit minimal wear, contributing to a prolonged lifespan of the valve. This durability not only results in cost savings for the end user but also ensures steady performance over time.
Minimal Pressure Drop
A standout benefit of ball valves is their minimal pressure drop, a feature that sets them apart from other valve types. Thanks to the spherical closure’s streamlined flow path, fluid movement is smooth and unrestricted, leading to minimal pressure loss throughout the valve. This characteristic is especially advantageous in scenarios where it’s crucial to maintain consistent fluid pressure, as it helps reduce energy consumption and enhances system efficiency.
In summary, the combination of full shut-off capabilities, low maintenance, high durability, and minimal pressure drop positions ball valves as a dependable option for fluid control systems in a wide array of industries.
Choosing the Right Valve for Your Application
This, therefore, calls for the need to make a very important consideration in selecting the right type of valve for your application, given the very critical role it will play toward achieving the best performance within your system.
Thus, there are quite a number of factors when comparing a globe valve with a ball valve that need to be weighed, and the same may bear fruit over the efficiency and effectiveness of the operations.
Factors to Consider
When selecting a valve for a specific application, it’s essential to evaluate the following factors:
- Flow Control Requirements: Take into consideration the jsonaritic flow and establish if precise control or on-off service requirement is needed.
- Pressure and Temperature: Investigate the system’s operating pressure and temperature conditions to find out whether this coincides with the pressure, temperature, and relative temperature limits of the selected valve.
- Fluid Compatibility:
It is used to ascertain the kind of fluid being handled and gives a choice of material for the valve, which is also corrosion- or erosion-resistant. - Maintenance and Repair:
Evaluate the availability of the selected valve and ease of service, thus achieving minimum downtime at a reduced maintenance cost.
Globe Valve or Ball Valve
Both globe valves and ball valves offer unique advantages based on the specific requirements of an application:
Globe Valve
Globe valves are ideal for applications that require fine throttling and regulating flow. The globe valves are very appropriate where systems require the regulation of flow rates because of their ability to control.
https://www.sciencedirect.com/topics/engineering/globe-valve
Due to design, the globe valve provides suitable conditions for temperature and pressure control since it is capable of resisting conditions, even where the service is most likely to change.
However, generally, with the particular nature of globe valves, they had much more pressure drops when compared to ball valves, thus decreased the efficiency of the system.
Ball Valve
Ball valves are renowned for their quick and reliable on/off control of flow.
They are well suited for the applications which are full bore and unrestricted flow when open, and tight shut-off when closed. Some of the advantages are that ball valves will serve the purpose when put in the system where little pressure drop and a priority of reduced maintenance takes place. Ball valves are having lesser precision in control capabilities than globe valves and are the best choice for on/off function applications.
Finally, consideration of either globe valve or ball valve would be based on the requirement of the application to use precision in controlling flow, demands for pressure, temperature, compatibilities of fluids, and needs for maintenance.
Any valve is not selected directly from the manufacturer, but it has a set of unique benefits. Proper selection of valves will serve for performance and serviceability in your system.
Conclusion on Globe Valve vs. Ball Valve
In brief, consideration has to be taken of the kind of flow control, head loss, valve design, and some of the special application requirements whenever there is a selection between a globe or ball valve for a given system.
As a rule, globe valves are more appropriate in applications where there is a necessity for fine flow control and a higher pressure drop, while a ball valve is best suited for on/off control with a minimal pressure drop. Each of these valves possesses some advantages and disadvantages; selection of any one of these can be made by evaluating the needs of the system.
Explaining the working principles and differences between a globe valve and a ball valve, therefore, enables one to decide from an informed point of view on the type of valve to use in the piping system to make sure that it serves them efficiently and their purposes adequately.