Comparing the Performance of Wafer Check Valves in Different Operating Conditions
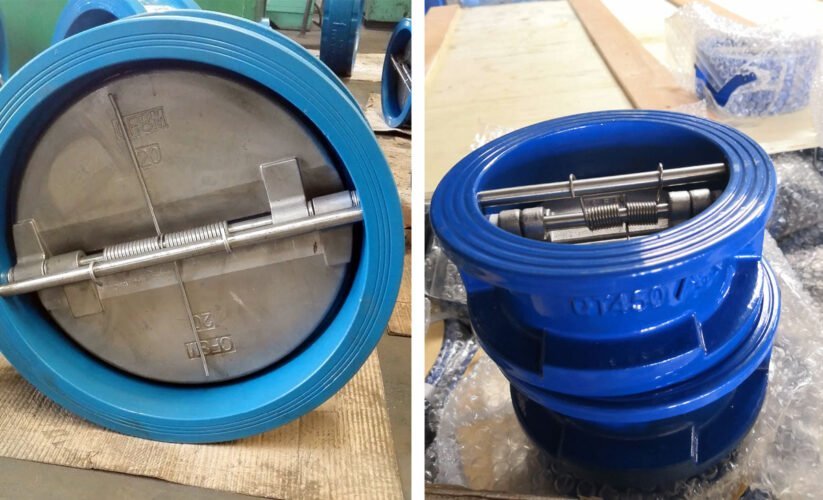
Table of Contents
ToggleExamining Wafer Check Valve Performance Across Diverse Operating Conditions
From extreme temperatures to varying pressure levels, the performance of wafer check valves can significantly impact industrial operations. In this blog post, we will evaluate the performance of wafer check valves across diverse operating conditions, equipping you with the knowledge to optimize their usage in your facility.
- Performance of Wafer Check Valves in Different Operating Conditions
- In vertical flow conditions, wafer check valves have shown to perform efficiently by preventing backflow and maintaining a steady flow rate.
- When installed in horizontal pipelines, wafer check valves have demonstrated the ability to effectively prevent backflow and minimize pressure drop.
- In low-pressure systems, wafer check valves have displayed reliable performance by preventing backflow and ensuring minimal resistance to flow.
- In high-pressure environments, wafer valves have proven to effectively prevent backflow and maintain structural integrity without compromising performance.
- Across varying temperatures, wafer check valves have maintained consistent performance by preventing backflow and withstanding thermal stress.
- In corrosive or abrasive media, wafer valves have exhibited resilience by preventing backflow and resisting wear and tear, contributing to extended operational lifespan.
- When exposed to rapid cycling or frequent operation, wafer check valves have sustained reliable performance by preventing backflow and enduring mechanical stress.
- In applications requiring low maintenance, wafer valves have shown to be advantageous by offering consistent performance in preventing backflow without frequent servicing.
Overview of Wafer Check Valves
Wafer check valves are vital components in fluid control systems, designed to prevent backflow and safeguard pipelines from damage. Their compact and lightweight design makes them suitable for various applications. By understanding their functionalities, it’s possible to gain insights into the significant role that wafer check valves play in different industries.
What is a Wafer Check Valve?
Wafer check valves are mechanical devices that permit fluid discharge in one direction while preventing backflow in the opposite one. They are installed between two flanges, providing a space-saving and compact design. There are various types of wafer check valves, including swing check valves and dual plate check valves. Swing check valves feature a hinged disc that swings open to allow forward discharge and swings shut to prevent backflow. On the other hand, dual plate check valves consist of two plates that open and close in response to the flow direction, offering a compact design and fast response time.
Design and Features of Wafer Check Valves
These valves operate based on the principle of fluid pressure and flow direction. When fluid flows in the desired direction, the force of the flow lifts the check valve’s disc, enabling the fluid to pass through. However, in the event of reverse flow or backflow, the disc closes, preventing the fluid from flowing backward and protecting the system from damage. Additionally, one of the significant aspects to consider when using wafer valves in systems is the valve size and weight. The correct sizing and weight are crucial in ensuring optimal performance and efficiency within the system.
Significance of Valve Size and Weight in Systems
The size and weight of wafer check valves are crucial considerations in various systems. Proper sizing and weight ensure that the valves effectively handle the flow of fluids, preventing backflow and protecting the system. Selecting the right valve size and weight is essential for maximizing the performance and reliability of the entire system.
Operating Principles of Wafer Check Valves
Wafer check valves are crucial components in various industrial applications, relying on the intricate interplay of a few key principles to ensure smooth and reliable operation. Spring assistance is a fundamental aspect that significantly impacts the performance of wafer check valves. The presence of a spring within the valve assembly aids in maintaining proper seating and sealing of the valve disc. The spring assists in providing the necessary force to ensure the valve remains closed until the pressure exceeds a predetermined threshold, preventing backflow and safeguarding the integrity of the system.
The Role of Spring Assistance in Valve Performance
The spring within a wafer check valve serves as a vital element in dictating its functionality. When the flow of fluid comes to a halt, the spring assists in promptly closing the valve to prevent any reverse flow. This mechanism minimizes the risk of potential damage to downstream equipment, preserving the overall integrity of the system. By providing the necessary force to ensure swift closure, the spring effectively maintains the efficiency and reliability of the wafer check valve, making it a critical component in various industrial processes.
Response to Flow Direction Changes
Another essential aspect of the operating principle of wafer check valves is their responsive nature to flow direction changes. When the fluid flow changes direction, the valve promptly adjusts to allow the flow while effectively preventing backflow. This responsive behavior is crucial in maintaining the desired flow direction within the system, ensuring optimal performance and operational efficiency. The seamless adaptation to flow changes underscores the agility and reliability of wafer check valves, making them indispensable in diverse industrial settings.
In summary, the spring assistance in wafer check valves plays a pivotal role in ensuring efficient performance and system reliability, while their responsive behavior to flow direction changes further reinforces their importance in various industrial applications. Understanding these operating principles is essential for optimizing the usage of wafer check valves across different operating conditions.
Varied Operating Conditions for Wafer Check Valves
In various industries, wafer check valves are utilized to control the flow of fluids in different operating conditions. These valves are commonly employed in:
Where is wafer check valve used?
- Chemical Industry: For regulating the flow of corrosive liquids and gases.
- Oil and Gas Sector: To manage the flow within pipelines and refineries.
- Water Treatment Plants: For controlling the passage of water and wastewater.
High-Pressure Environments
In high-pressure environments such as industrial settings and hydraulic systems, wafer check valves play a crucial role. These valves are designed to withstand and manage the elevated pressure levels, ensuring efficient fluid control and preventing any potential damage to the system.
Rapid Flow Scenarios
Wafer check valves are well-suited for rapid flow scenarios where the fluid velocity is high. Their quick response time and ability to handle rapid flow conditions make them an ideal choice for applications requiring swift and efficient fluid regulation.
Presence of Particulates and Debris
In environments with the presence of particulates and debris, wafer check valves demonstrate their reliability by effectively preventing the entry of solid particles into the system. Their design and operational mechanism ensure that the flow remains unobstructed, contributing to the overall efficiency and longevity of the fluid control system.
In summary, the adaptability of wafer check valves across varied operating conditions underscores their versatility and effectiveness in ensuring optimal fluid control and system protection.
Performance Metrics for Wafer Check Valves
Wafer check valves are critical components in various industries, ensuring fluid flow in one direction while preventing backflow. Assessing their performance in different operating conditions involves evaluating key metrics such as backflow prevention capabilities, durability, and lifespan.
Assessing Backflow Prevention Capabilities
The effectiveness of wafer check valves in preventing backflow is a crucial performance metric. Factors such as pressure differentials, flow rates, and fluid properties must be considered to ensure optimal backflow prevention. These valves need to maintain a secure seal to prevent any reverse flow, especially in scenarios with varying flow rates or fluctuating pressures. The ability of wafer check valves to consistently prevent backflow under diverse operating conditions is a significant indicator of their performance.
Durability and Lifespan in Different Conditions
Another essential metric for evaluating wafer check valve performance is durability and lifespan under different operating conditions. These valves are exposed to varying fluid pressures, temperatures, and flow rates, which can impact their overall longevity. Assessing how wafer check valves withstand harsh operating environments, corrosion, erosion, and thermal stress is vital. Understanding their expected lifespan under different conditions enables industries to make informed decisions regarding maintenance schedules and replacement intervals, contributing to overall operational efficiency.
In summary, assessing the performance metrics of wafer check valves involves a comprehensive evaluation of their backflow prevention capabilities, durability, and lifespan in diverse operating conditions. By understanding and optimizing these key metrics, industries can ensure the reliable and efficient operation of wafer check valves across various applications.
Comparison with Other Check Valves
Wafer vs Swing Check Valves in Fluid Dynamics
When comparing wafer and swing check valves in terms of fluid dynamics, it’s essential to consider the flow characteristics and pressure drop. Wafer check valves are designed to provide a low-pressure drop and are suitable for applications requiring high flow rates. On the other hand, swing check valves are known for their ability to minimize turbulence and pressure surges in the system, making them ideal for applications where fluid dynamics play a crucial role in overall system performance.
Cost-Effectiveness
In terms of cost-effectiveness, wafer check valves often prove to be more economical than swing check valves. The installation and maintenance costs for wafer check valves are relatively lower, making them a cost-effective choice for many applications. Swing check valves, while offering durability and robustness, may incur higher initial and maintenance costs, especially in applications that require frequent inspection and maintenance.
Long-Term Value
When considering long-term value, both wafer and swing check valves have their merits. Wafer check valves, due to their lower installation and maintenance costs, may present a higher long-term value in applications where cost efficiency is a priority. Conversely, swing check valves, with their robust construction and durability, offer long-term reliability and extended service life, making them a valuable choice for applications where longevity and minimal downtime are critical factors.
In conclusion, the choice between wafer and swing check valves depends on specific operational requirements, fluid dynamics considerations, budget constraints, and the overall lifecycle cost. Understanding the distinct advantages of each type of check valve empowers system engineers and facility managers to make informed decisions that align with the operational and financial objectives of their systems.
Customization and Adaptability
Material Selection for Specific Environments
Selecting the appropriate materials for wafer check valves is critical for ensuring optimal performance in different operating conditions. When faced with corrosive or abrasive media, it’s essential to choose materials that offer high resistance to corrosion and erosion. For instance, in environments with high acidity, stainless steel or alloy materials may be preferred due to their corrosion-resistant properties. On the other hand, applications involving high temperatures and pressures could demand materials with high tensile strength and thermal stability, such as titanium alloys or specialized polymers. By customizing the material selection based on specific environmental factors, the performance and longevity of wafer check valves can be significantly enhanced.
Modifications for Unique System Requirements
In certain instances, off-the-shelf wafer check valve configurations may not fully meet the unique system requirements of certain applications. In such cases, the adaptability of wafer check valves through modifications becomes crucial. This may involve adjusting the valve’s dimensions to fit within confined spaces, or incorporating additional features such as sealing enhancements to improve leak-tightness. Furthermore, the integration of specialized coatings or linings on valve components can be employed to provide protection against aggressive media or to minimize frictional losses. Custom modifications tailored to the specific needs of the system contribute to improved operational efficiency and reliability, showcasing the adaptability of wafer check valves in accommodating diverse application demands.
Installation Considerations for Wafer Check Valves
How is a wafer check valve installed?
Wafer check valves are typically installed between flanges using bolts and nuts to secure them in place. The valve is designed to fit between standard flanges, making it a compact and space-efficient choice for various piping systems.
Space Constraints and System Compatibility
When considering the installation of wafer check valves, it is crucial to assess the available space between flanges. The compact design of these valves makes them suitable for systems with limited space. Additionally, it is essential to ensure that the system is compatible with wafer check valves, taking into account factors such as flow direction and pressure ratings.
Installation Best Practices for Optimal Performance
To ensure optimal performance, it is important to follow best practices during the installation of wafer check valves. This includes proper alignment between the valve and flanges, ensuring that the valve is secured tightly in place, and verifying that the system is free from any debris that could affect the valve’s functionality. Additionally, attention should be given to the orientation of the valve to ensure that it functions as intended within the system.
Maintenance and Troubleshooting
Maintenance troubleshooting is a critical aspect of ensuring the optimal performance of wafer check valves in various operating conditions. By understanding the regular maintenance needs, common issues, and solving techniques, maintenance professionals can effectively uphold the functionality of these valves.
Regular Maintenance Needs
When it comes to wafer check valves, regular maintenance plays a pivotal role in preventing unexpected breakdowns and ensuring continuous operation. This involves inspecting the valves for any signs of wear, corrosion, or leakage, and addressing these issues promptly. Additionally, lubrication and cleaning of the valves are essential to maintain their efficiency and longevity.
Common Issues and Solving Techniques
Common issues that may arise with wafer check valves include leakage, reduced sealing effectiveness, and decreased flow control. When encountering these issues, maintenance technicians can employ various solving techniques. This includes resealing the valves, replacing damaged components, and adjusting the pressure settings to optimize performance.
By staying proactive with regular maintenance and having a clear understanding of common issues and their solving techniques, maintenance professionals can effectively uphold the operational efficiency of wafer check valves, thereby minimizing downtime and optimizing overall performance.
FAQ: Comparing the Performance of Wafer Check Valves in Different Operating Conditions
What are the key differences between wafer check valves and traditional check valves?
Traditional check valves, known as swing check valves, have a bulkier body design, requiring more installation space. Wafer check valves, on the other hand, are designed for compact spaces, making them ideal for applications with limited space.
What are the advantages of using wafer check valves?
Wafer check valves offer an all thermoplastic design that eliminates environmental corrosion, making them lighter than metal and highly durable against mechanical, physical, and chemical wear.
What are the consequences of a poorly functioning check valve?
Poorly functioning check valves can lead to issues such as noise and vibration from water hammer, reverse flow, leakage, or damage. Sticking valves may occur due to the presence of scale or debris trapped between the valve body and moving parts like the disc or ball.
Should wafer check valves be installed vertically or horizontally?
Wafer lift check valves are not suitable for vertical installation and should only be installed on horizontal pipelines.
Conclusion
Conclusion 1: The Superiority of Wafer Check Valves in Low-Pressure Environments
In low-pressure operating conditions, it is evident that wafer check valves outperform other valve types in terms of efficiency and reliability. Their compact design and minimal pressure drop make them an ideal choice for applications with low-pressure requirements.
Conclusion 2: The Impact of Fluid Velocity on Wafer Check Valve Performance
When comparing wafer check valves in different operating conditions, the influence of fluid velocity becomes apparent. These valves exhibit exceptional performance in high-velocity environments, showcasing their ability to effectively control the flow of fluids and prevent backflow.
Conclusion 3: Thermal Stability and Wafer Check Valves
In scenarios involving temperature variations, wafer check valves demonstrate remarkable thermal stability, maintaining their functionality and integrity. This makes them a reliable choice for applications where temperature fluctuations are a concern, ensuring consistent performance and safety.
Conclusion 4: The Overall Versatility of Wafer Check Valves
In conclusion, the comprehensive evaluation of wafer check valves in different operating conditions highlights their versatility and adaptability. Whether it’s low-pressure, high-velocity, or thermal fluctuation, these valves consistently prove to be a dependable solution for diverse industrial settings.