Successful Applications of Tilting Disc Check Valves in Oil and Gas Industry
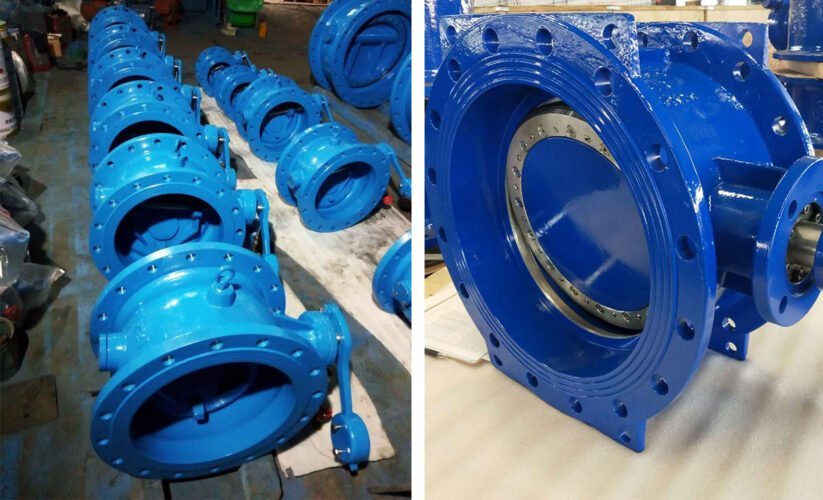
The application of tilting disc check valves in the oil and gas industry has proven to be successful in various scenarios. Case studies across different sectors within the industry, such as natural gas, petroleum production refining, and power generation, demonstrate the effectiveness of these valves in addressing specific challenges. From issues like low flow and excessive cycling to water hammer and high flow lockout, the versatility of tilting disc check valves in mitigating operational challenges is evident. This blog post will delve into these case studies, highlighting the successful applications of tilting disc check valves in the oil and gas industry.
Table of Contents
ToggleUnderstanding Tilting Disc Check Valves
- Tilting disc check valves are crucial components in the oil and gas industry due to their ability to prevent backflow and protect critical equipment.
- These valves are designed to allow flow in one direction while preventing reverse flow, thus maintaining the integrity of the system.
- Tilting disc check valves are commonly used in high-pressure and high-temperature applications, making them ideal for the demanding conditions of the oil and gas industry.
- The unique tilting disc design allows for quick response to flow changes, reducing the risk of water hammer and potential damage to the system.
- These valves are typically constructed from durable materials such as stainless steel or alloy steel to withstand the harsh operating conditions encountered in the oil and gas industry.
- Proper installation and maintenance of tilting disc check valves are critical to ensure optimal performance and reliability in oil and gas applications.
- In conclusion, tilting disc check valves play a vital role in maintaining the safety and efficiency of oil and gas systems by preventing backflow and safeguarding equipment from damage.
Basic Function and Design
Tilting disc check valves are designed to regulate the flow of fluids within a pipeline. The basic functioning involves the rotation of a disc to allow or prevent the flow of fluids based on the pressure within the pipeline. The unique design of the tilting disc allows for efficient control of fluid flow and prevents backflow, ensuring smooth operation within oil and gas applications.
Comparison with Other Check Valve Types
In comparison to other check valve types such as swing check valves or lift check valves, the tilting disc check valves demonstrate superior performance in oil and gas applications. Their quick closing mechanism reduces the risk of water hammer, a common concern in pipeline systems. Moreover, the streamlined flow path and reduced turbulence result in energy savings and prolonged equipment lifespan. Overall, the tilting disc check valves prove to be a reliable and efficient choice for check valve applications in the oil and gas industry.
The Benefits of Tilting Disc Check Valves in the Oil and Gas Industry
In oil and gas industry environments, the tilting disc check valves offer several advantages. Their robust design and ability to handle high-pressure systems make them suitable for demanding applications. The self-cleaning mechanism of the tilting disc ensures reliable performance, even in scenarios with the presence of contaminants or debris. Furthermore, the minimal pressure drop across the valve enhances the overall efficiency of the system, making it a preferred choice in oil and gas operations.
Advantages of Tilting Check Valves
- Enhanced Flow Control: Tilting disc check valves are designed to provide excellent flow control in high-pressure and high-velocity applications commonly found in the oil and gas industry. The tilting disc design allows for smooth and unobstructed flow, reducing pressure drop and minimizing the risk of valve failure.
- Superior Reliability: One of the most significant benefits of tilting disc check valves is their exceptional reliability. The robust construction and advanced sealing mechanisms of these valves make them highly resistant to wear, erosion, and corrosion, ensuring long-term performance and minimal maintenance requirements in demanding oil and gas environments.
- Preventing Reverse Flow: In oil and gas systems, preventing reverse flow is crucial for maintaining operational efficiency and safety. Tilting disc check valves are specifically engineered to prevent backflow, effectively safeguarding critical equipment and processes from potential damage and ensuring uninterrupted flow in the intended direction.
- Minimal Pressure Loss: Tilting disc check valves are designed to minimize pressure loss, making them ideal for applications where efficient energy transfer is essential. By reducing pressure drop across the valve, these valves help optimize system performance and contribute to overall energy efficiency in oil and gas operations.
- Compatibility with Harsh Environments: Oil and gas environments are often characterized by extreme temperatures, high pressures, and corrosive substances. Tilting disc check valves are built to withstand these harsh conditions, featuring materials and coatings that provide exceptional resistance to erosion, abrasion, and chemical attack, ensuring reliable performance in challenging operational settings.
Tilting disc check valves play a critical role in ensuring the safety, efficiency, and reliability of oil and gas operations. Their unique design and performance characteristics make them indispensable components in a wide range of applications within the industry, demonstrating their capability to meet the stringent demands of oil and gas systems.
Case Study 1: Enhancing Safety in Natural Gas Compressor Stations
Compressor stations play a vital role in maintaining the flow and pressure of natural gas within the pipeline network. However, with this crucial function comes the responsibility of ensuring safety and efficiency within these facilities.
Problem
The use of traditional check valves in natural gas compressor stations posed safety risks due to their susceptibility to failure under high-pressure and high-velocity conditions. These failures could lead to significant damage to equipment and potential safety hazards, including gas leaks and operational downtime.
Solution
The implementation of tilting disc check valves offered a reliable solution to the safety concerns associated with traditional check valves. The unique design of tilting disc check valves allows them to withstand high-pressure and high-velocity gas flows, ensuring uninterrupted and secure operations within the compressor stations.
Benefits
The integration of tilting disc check valves brought about several notable benefits, including enhanced operational safety, reduced maintenance requirements, and minimized downtime due to valve failures. Additionally, the improved efficiency of flow control led to cost savings and increased overall productivity within the compressor stations.
Outcomes
Following the installation of tilting disc check valves, the compressor stations experienced a significant reduction in safety incidents related to valve failures, contributing to a safer working environment for personnel. Moreover, the enhanced performance and reliability of the valves resulted in improved operational continuity and a notable decrease in maintenance-related expenses.
By addressing the safety concerns associated with traditional check valves, the implementation of tilting disc check valves in natural gas compressor stations has proven to be a pivotal step towards ensuring operational safety, efficiency, and cost-effectiveness within the oil and gas industry.
Case Study 2: Optimizing Petrochemical Processing
Problem
In the petrochemical industry, process efficiency is critical for maintaining competitiveness and meeting growing demands. Our client, a major petrochemical company, was facing challenges with their existing check valve solutions. The conventional valves were causing frequent disruptions in the processing line, leading to costly downtime and maintenance. The inefficiencies were impacting the overall production output and increasing operational costs.
Solution
To address the operational challenges, our team recommended the implementation of tilting disc check valves. These valves are specifically designed to provide reliable and uninterrupted flow control in demanding petrochemical processing environments. The unique design of the tilting disc valve ensures minimal turbulence and pressure drop, thereby optimizing the flow efficiency and reducing the likelihood of valve-related issues.
Results
Following the installation of the tilting disc check valves, the petrochemical processing plant experienced a significant improvement in operational efficiency. The new valves effectively minimized flow disruptions and pressure differentials, resulting in reduced downtime and maintenance requirements. The enhanced flow control capability of the tilting disc valves contributed to a notable increase in production output and a substantial reduction in operational costs for the client. The successful application of tilting disc check valves demonstrated their ability to optimize petrochemical processing operations, underscoring their value as a reliable and efficient solution for the industry.
Case Study 3: Improving Petroleum Production and Refining
Problem
In the petroleum production and refining industry, the existing check valve solutions were causing frequent downtime and maintenance issues. The conventional swing and lift check valves were unable to provide reliable and efficient performance in the harsh operating conditions of the oil and gas industry. This led to significant production losses and increased operational expenses.
Solution
The implementation of tilting disc check valves offered a promising solution to the operational challenges faced by the petroleum production and refining facilities. The unique design of tilting disc check valves ensures a streamlined flow path and reduced turbulence, leading to improved operational efficiency and decreased maintenance requirements. The high-performance materials used in the construction of these valves also make them well-suited for the corrosive and abrasive nature of petroleum products.
Results
Following the installation of tilting disc check valves, the petroleum production and refining facilities experienced a remarkable improvement in operational reliability. The reduction in downtime and maintenance requirements resulted in substantial cost savings for the facilities. Additionally, the optimized flow characteristics of the valves contributed to enhanced production output and overall process efficiency. The successful application of tilting disc check valves demonstrated their potential to positively impact the operational performance of the oil and gas industry.
Case Study 4: Managing Waste Water Treatment in Refineries
Problem
Refineries face the challenge of managing and treating wastewater, which contains various contaminants such as oil, grease, BOD, COD, and suspended solids. These contaminants need to be significantly reduced to meet pollution control board standards for discharge.
Solution
The effluent treatment plant (ETP) at a refinery in the western region of India implemented monitoring and performance evaluation studies. Samples from the inlet and outlet locations of the ETP were collected at regular intervals and analyzed for different parameters. Through this process, the plant aimed to effectively treat the wastewater and reduce the levels of pollutants to meet regulatory standards.
Outcomes
The generated data from the monitoring and performance evaluation studies indicated a significant reduction in pH, oil & grease, BOD, COD, and suspended solids. This evidence demonstrated that the refinery’s ETP was operating within the norms specified by the pollution control board, thereby meeting the discharge standard requirements.
This successful application of wastewater treatment in refineries showcases the importance of implementing efficient treatment processes to ensure environmental compliance and the sustainable operation of refineries.
Operational Benefits of Tilting Disc Check Valves in the Oil and Gas Industry
Reducing Downtime and Maintenance Costs
Tilting disc check valves offer significant operational benefits in the oil and gas industry. Their quick-closing system effectively reduces downtime by swiftly responding to backflow, preventing damage to critical equipment and minimizing the need for unscheduled maintenance. This not only saves time but also reduces maintenance costs, enhancing overall operational efficiency.
Improving System Lifespan and Reliability
The design of tilting disc check valves allows for rapid opening and closing, ensuring superior performance under varying flow conditions. This, in turn, helps to stabilize low and pulsating flows, leading to a moderate drop in pressure and tight metal seat sealing. The stability and reliability provided by these valves contribute to prolonged system lifespan and overall operational integrity.
Enhancing Performance Under Varying Flow Conditions
The unique design of tilting disc check valves enables them to open at a medium speed, preventing disc “hammering” at low speeds and minimizing wear on critical components. With the ability to respond quickly to flow changes, these valves ensure stable and efficient performance across a wide range of flow conditions, making them suitable for applications requiring swift and reliable responses.
Selection Criteria for Tilting Disc Check Valves in Oil and Gas
When selecting tilting disc check valves for oil and gas applications, several factors should be considered to ensure optimal performance and reliability. The following criteria play a crucial role in the selection process:
Factors to Consider When Choosing Valves
- Flow Rate and Pressure: Evaluate the anticipated flow rates and operating pressures within the oil and gas system to select a tilting disc check valve that can accommodate these conditions without compromising performance.
- Corrosion Resistance: Given the corrosive nature of many oil and gas mediums, it’s essential to choose materials that offer superior resistance to corrosion, erosion, and other detrimental effects, ensuring long-term durability and functionality.
- Maintenance Requirements: Consider the ease of maintenance and potential downtime associated with the valve, opting for designs that facilitate straightforward inspection, repair, and replacement procedures for enhanced operational efficiency.
- Reliability and Longevity: Prioritize valves with a proven track record of reliability in similar oil and gas environments, as well as those known for their longevity and minimal susceptibility to premature failure.
Customization Options for Specific Applications
- Material Selection: Manufacturers often offer customization in terms of valve materials to align with the specific chemical composition and properties of the oil and gas being transported, mitigating the risk of material degradation and ensuring compatibility.
- Pressure Class and Size: Tailoring the pressure class and valve size to suit the unique requirements of the oil and gas system can optimize performance and efficiency, allowing for seamless integration and operation within the existing infrastructure.
- Sealing Mechanisms: Customizable sealing arrangements, such as soft or metal-to-metal seals, enable the adaptation of tilting disc check valves to varying temperature and pressure conditions, enhancing their effectiveness across a spectrum of oil and gas applications.
By carefully evaluating these selection criteria and exploring the available customization options, oil and gas industry professionals can effectively identify and deploy tilting disc check valves that align with the specific demands of their operations, promoting reliability, longevity, and operational resilience.
FAQs: Tilting Disc Check Valves
What are tilting disc check valves and how are they used in the oil and gas industry?
Tilting disc check valves are mechanical devices used to control the flow of fluids in a single direction. In the oil and gas industry, these valves are essential for preventing backflow, ensuring the safety and efficiency of pipelines and systems.
What makes tilting disc check valves suitable for oil and gas applications?
Tilting disc check valves are preferred in the oil and gas industry due to their ability to handle high-pressure and high-velocity flows, along with their capability to operate in harsh and demanding conditions.
What are the key benefits of using tilting disc check valves in the oil and gas sector?
Tilting disc check valves offer low-pressure drop, a tight shut-off, and reduced water hammer effects. They also provide reliable performance, reduced maintenance needs, and long service life, making them ideal for critical applications in the oil and gas industry.
How do tilting disc check valves contribute to safety and environmental protection in oil and gas operations?
By preventing reverse flow of hazardous fluids, tilting disc check valves play a crucial role in maintaining the integrity of pipelines and preventing potential environmental hazards. They help ensure compliance with safety regulations and mitigate the risk of accidents.
What are some common considerations when selecting tilting disc check valves for oil and gas applications?
Factors to consider include valve size, pressure rating, material compatibility, flow capacity, and adherence to industry standards and regulations. Proper selection and installation are imperative for optimal performance and safety in oil and gas operations.
Conclusion
In conclusion, the successful applications of tilting disc check valves in the oil and gas industry have demonstrated their effectiveness in addressing various challenges across different sectors. From building maintenance to natural gas and petrochemical industries, these case studies have showcased the valves’ ability to mitigate issues such as low flow, water hammer, pressure spikes, and excessive wear.
The diverse range of applications, including cooling tower systems, mine dewatering, and turbine installations, underscores the versatility and reliability of tilting disc check valves in enhancing operational efficiency and reducing maintenance costs within the oil and gas sector. As the industry continues to evolve, the successful adoption of these valves in real-world scenarios serves as a testament to their instrumental role in ensuring the integrity and performance of critical equipment and processes.