Importance of Nozzle Check Valves in Water Pipeline Systems
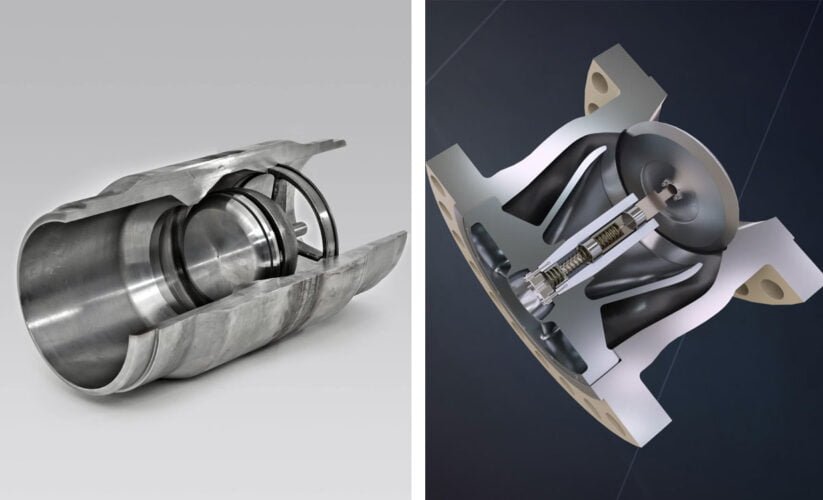
Table of Contents
ToggleIntroduction
Nozzle check valves play a crucial role in maintaining pressure stability in water pipeline systems. These valves are designed to prevent reverse flow and ensure that the pressure within the pipeline remains consistent. In this blog post, we will explore the importance of nozzle check valves in maintaining the integrity and efficiency of water distribution systems.
The Importance of Pressure Stability in Water Pipeline Systems
Pressure stability is a critical factor in the efficient functioning of water pipeline systems. Understanding pressure fluctuations and the consequences of inconsistent pressure is crucial for ensuring the reliability and longevity of the entire network.
Understanding Pressure Fluctuations
Water pipeline systems are designed to operate within specific pressure ranges to facilitate the seamless distribution of water to consumers. Fluctuations in pressure can occur due to various factors such as changes in demand, pipe blockages, or pump malfunctions. These fluctuations can lead to inefficiencies in the system and affect the overall delivery of water to end users.
Consequences of Inconsistent Pressure
Inconsistent pressure within water pipeline systems can have detrimental effects on the infrastructure and the quality of water delivery. Pressure surges or drops can cause stress on the pipeline components, leading to potential leaks, bursts, or corrosion. Moreover, fluctuating pressure can impact the performance of water treatment processes, resulting in compromised water quality for consumers. Additionally, varying pressure levels can affect the functionality of household appliances and industrial machinery connected to the water supply.
By comprehending the significance of maintaining pressure stability and the potential repercussions of pressure fluctuations, water utility operators can implement strategies to mitigate these issues and ensure a reliable and efficient water distribution system.
Nozzle Check Valves: Function and Design
How Nozzle Check Valves Work
Nozzle check valves, also known as non-return valves, play a crucial role in maintaining pressure stability within water pipeline systems. These valves are designed to allow fluid to flow in one direction while preventing backflow, ensuring that there is no loss of pressure within the system. When water flows through the nozzle check valve in the designated direction, the internal mechanism opens to allow passage. Conversely, when there is a reversal in flow direction or when pressure decreases, the valve closes to prevent the backflow of water. This crucial function ensures the integrity and efficiency of the pipeline system.
Types of Nozzle Check Valves
There are different types of nozzle check valves designed to cater to specific operational requirements. The most common types include swing check valves, lift check valves, and inline check valves. Each type has its unique design and functionality, offering versatility in applications depending on factors such as flow rate, installation orientation, and space limitations. Understanding the distinct features of each type is essential in selecting the most suitable valve for a particular water pipeline system.
Material and Size Considerations
The material composition and size of nozzle check valves are significant factors in their effectiveness and longevity. These valves are commonly constructed from materials such as stainless steel, brass, and PVC, each offering varying degrees of corrosion resistance and durability. The selection of material depends on the specific requirements of the water pipeline system, including the nature of the transported fluid and environmental conditions. Additionally, the size of the valve must align with the pipeline’s dimensions and flow capacity to achieve optimal performance and pressure stability. Proper consideration of material and size aspects is essential in ensuring the reliable functionality of nozzle check valves within water pipeline systems.
The Advantages of Nozzle Check Valves in Water Pipeline Systems
Water pipeline systems are crucial for ensuring the efficient transportation of water from one place to another. Nozzle check valves play a vital role in maintaining the integrity and functionality of these systems. Here are the advantages of utilizing nozzle check valves in water pipeline systems:
- Prevention of Backflow: Nozzle check valves are designed to prevent the backward flow of water within the pipeline system. This is essential for maintaining the direction of water flow and preventing contamination of the water supply.
- Reduced Water Hammer: Water hammer, caused by sudden changes in the flow of water, can lead to significant pressure surges within the pipeline. Nozzle check valves help mitigate water hammer effects by providing a controlled closure mechanism, thus reducing the risk of damage to the pipeline system.
- Enhanced System Efficiency: By maintaining the desired flow direction and minimizing pressure fluctuations, nozzle check valves contribute to the overall efficiency of water pipeline systems. This results in reduced energy consumption and operational costs.
- Protection of Equipment and Infrastructure: The installation of nozzle check valves helps protect pumps, pipes, and other system components from potential damage caused by backflow or water hammer, thereby extending the lifespan of the infrastructure.
- Compliance with Regulatory Standards: Many regulatory standards and codes require the use of check valves in water pipeline systems to ensure safety, reliability, and environmental protection. Nozzle check valves help operators and system owners meet these compliance requirements.
- Versatile Application: Nozzle check valves are suitable for a wide range of water pipeline systems, including municipal water distribution, industrial water treatment, agricultural irrigation, and wastewater management. Their versatility makes them an ideal choice for various applications.
- Minimal Maintenance Requirements: Nozzle check valves are designed for minimal maintenance, providing long-term reliability and operational peace of mind for system operators. This reduces the need for frequent interventions and associated downtime.
In conclusion, the advantages of incorporating nozzle check valves in water pipeline systems are evident in their ability to prevent backflow, reduce water hammer, enhance system efficiency, protect equipment, ensure regulatory compliance, offer versatile application, and require minimal maintenance. By leveraging these benefits, operators can optimize the performance and longevity of their water pipeline infrastructure.
Role of Nozzle Check Valves in Maintaining Pressure Stability
Preventing Backflow and Water Hammer
Nozzle check valves play a crucial role in maintaining pressure stability in water pipeline systems by preventing backflow and water hammer. When the flow direction reverses in a pipeline, backflow occurs, potentially causing contamination and damage to the system. Water hammer, on the other hand, is the sudden increase in pressure resulting from the abrupt stoppage of fluid flow. Nozzle check valves effectively mitigate these issues by allowing flow in one direction only, thus preventing backflow and reducing the risk of water hammer.
Ensuring Constant Pressure in the System
Nozzle check valves ensure a constant pressure in water pipeline systems by allowing flow in one direction only. This prevents pressure fluctuations that can occur due to backflow or sudden changes in flow velocity. By maintaining a consistent pressure, these valves contribute to the efficient and reliable operation of the entire pipeline system, reducing the risk of damage and ensuring consistent performance.
Impact on Overall System Efficiency
The presence of properly functioning nozzle check valves significantly impacts the overall efficiency of water pipeline systems. By preventing backflow and water hammer, these valves help maintain the integrity of the system, reducing the need for maintenance and repairs. Additionally, the consistent pressure maintained by these valves optimizes the performance of pumps and other equipment within the system, ultimately enhancing its overall efficiency and longevity.
Installation and Maintenance Best Practices for Nozzle Check Valves
Proper Placement in the Pipeline System
When installing nozzle check valves, it’s imperative to ensure proper placement within the water pipeline system. Placing the valve at strategic points where flow reversal needs to be prevented is crucial. These valves should be positioned in a manner that allows for optimal pressure stability while preventing backflow. Consulting with hydraulic engineers or industry experts during the installation process can help determine the most suitable locations within the pipeline for effective valve placement.
Regular Inspection and Testing
Regular inspection and testing are paramount to ensure the continued functionality of nozzle check valves in maintaining pressure stability. Setting up a routine inspection schedule, including visual checks for leaks, corrosion, and any signs of damage, can help identify potential issues early on. Additionally, conducting thorough testing of the valves to verify their performance under varying flow conditions is essential for preemptive maintenance and preventing system failures.
Addressing Common Issues and Failures
Nozzle check valves may encounter common issues and failures over time, impacting their ability to maintain pressure stability in water pipeline systems. Addressing these issues promptly is essential. Common problems such as debris accumulation, seal deterioration, or spring fatigue can be mitigated through regular maintenance and cleaning. Implementing proactive measures, such as installing strainers upstream of the valves to prevent debris buildup, can contribute to the longevity and effectiveness of the valves in upholding pressure stability.
Nozzle Check Valves in Water Pipeline Systems: FAQ
What is a nozzle check valve and how does it work?
A nozzle check valve uses a nozzle and disc arrangement to prevent backflow. The fluid flows in the correct direction, allowing the disc to move away from the nozzle, permitting fluid to pass through. In the case of backflow, the disc moves back towards the nozzle, effectively sealing off the valve and preventing further flow.
What are the advantages of using nozzle check valves in water pipeline systems?
Nozzle check valves provide a full-flow area with low pressure drop, making them ideal for high-flow applications. They are relatively simple and easy to maintain, which makes them a popular choice in many industries.
How do nozzle check valves differ from axial silent check valves?
Nozzle check valves use a nozzle and disc arrangement, while axial silent check valves use a spring-loaded disc to prevent backflow. Additionally, nozzle check valves are known for providing a full-flow area with low pressure drop, whereas axial silent check valves are designed to operate quietly and smoothly, without the characteristic “thump” of traditional check valves.
What type of applications are nozzle check valves best suited for in water pipeline systems?
Nozzle check valves are ideal for high-flow applications where low pressure drop and full-flow area are critical. They are commonly used in various industries, including water treatment, irrigation, and industrial processes.
What are the standard specifications for nozzle check valves in water pipeline systems?
Nozzle check valves typically adhere to the EN558 Series 14 standard for Face to Face length, which sets them apart from axial check valves that adhere to the EN558 Series 8 standard. This specification is crucial for understanding the size and material cost differences between the two types of check valves.
Conclusion
In conclusion, nozzle check valves play a crucial role in maintaining pressure stability in water pipeline systems. By preventing backflow and ensuring unidirectional flow, these valves help to optimize the performance and efficiency of the entire pipeline network. Their ability to minimize pressure loss and water hammer effects makes them indispensable in sustaining the integrity and functionality of water distribution systems. Understanding the significance of nozzle check valves in hydraulic operations is essential for ensuring the smooth and uninterrupted flow of water through pipelines.