High-Performance Butterfly Valves: Enhancing Oil and Gas Pipeline Operations
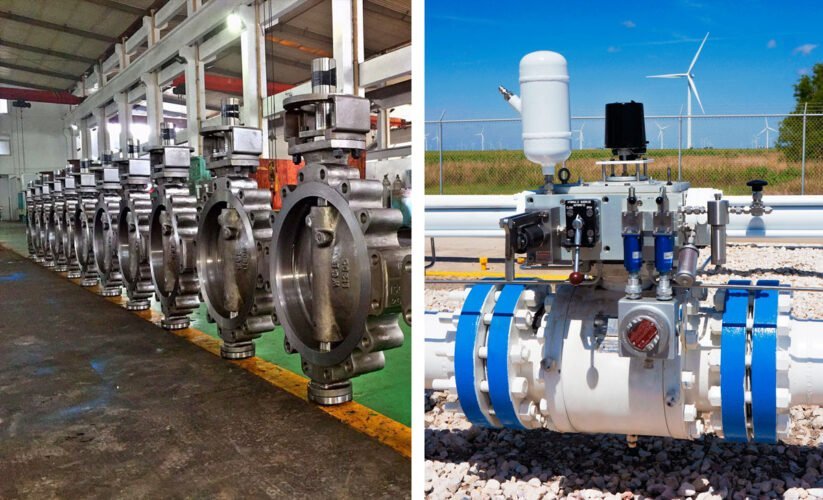
Table of Contents
ToggleFunctionality of High-Performance Butterfly Valves in Oil and Gas Pipeline Operations
In the ever-evolving industrial landscape, technology continues to advance, transforming the way fluid flow is controlled for improved operational efficiency. Butterfly valve technology exemplifies this progress, with recent innovations leading to the development of high-performance butterfly valves. These valves not only regulate fluid flow more effectively but also reduce energy loss and maintain system pressure, enhancing overall system efficiency.
Advancements in research and development have also led to the creation of energy-efficient and reliable butterfly valves designed specifically for high flow applications like HVAC systems. Furthermore, the use of advanced materials, coatings, and sealing technologies is contributing to the creation of more durable and efficient products. This ongoing innovation in butterfly valve technology not only improves flow control and efficiency but also promotes sustainability by reducing greenhouse gas emissions. As such, the future of butterfly valve technology promises even greater advancements, with the potential to revolutionize a wide range of industries.
The Evolution of Butterfly Valves in Flow Control
The Basics of Butterfly Valves in Pipelines
Butterfly valves have revolutionized flow control in pipelines since their introduction in the 1950s. Unlike traditional gate valves, butterfly valves are lighter, more compact, and offer a more effective shutoff method for regulating fluid flow. The design of butterfly valves features a concentric disc that rotates 90 degrees from fully closed to fully open, providing a streamlined approach to flow regulation.
Challenges with Conventional Butterfly Valves
While resilient seated butterfly valves initially served as a viable alternative to gate valves in low-pressure, low-temperature environments, they faced limitations when it came to withstanding higher temperatures and corrosive services. The industry’s increasing demands for more efficient and safer valves led to the emergence of high-performance butterfly valves.
Advances in Valve Technology for Oil and Gas Applications
Developments in high-performance butterfly valves addressed the need for enhanced durability and safety in flow control applications. The double-offset disc design of high-performance butterfly valves reduced wear on the seat, enabling them to withstand extreme temperatures and pressures, making them suitable for a wide range of industries. To further meet the demand for tight shutoff in critical applications, the triple-offset butterfly valve was developed, setting new standards for bidirectional zero leakage according to international standards. These advancements have significantly improved flow control in oil and gas pipelines, offering enhanced efficiency, safety, and longevity.
What is a High-Performance Butterfly Valve?
Key Features of High-Performance Butterfly Valves
High-performance butterfly valves are designed with several key features that set them apart from standard butterfly valves. These include a metal disc positioned within the valve’s body to control the flow of liquid or gas through a piping system. They are operated via handles, gears, or automatic actuators, making them versatile for various applications. These valves offer space efficiency and cost-effectiveness compared to other valve types, making them suitable for a wide range of industries.
The Role of Materials and Design in Performance
The materials and design of high-performance butterfly valves play a crucial role in their effectiveness. They are equipped with PTFE seats that can withstand chemically reactive and corrosive liquids and gases, distinguishing them from general service butterfly valves. The seat design ensures that the materials being processed do not come into contact with the body, making them suitable for vacuum applications. The advanced design and materials make these valves resilient in handling higher temperatures and pressure levels, up to 285 PSI and beyond.
Comparing Standard to High-Performance Butterfly Valves
When comparing high-performance butterfly valves to standard butterfly valves, it is evident that high-performance valves are engineered to handle a broader range of fluids and gases. They offer enhanced durability and can tolerate chemically reactive and corrosive substances, making them suitable for demanding applications that standard valves cannot accommodate. The ability to withstand higher pressures and temperatures makes high-performance butterfly valves indispensable in critical industrial processes, providing reliability and efficiency where standard valves fall short.
What Makes a Butterfly Valve High Performance
When to Use High-Performance Butterfly Valves
High performance butterfly valves are designed to handle the challenges of demanding process conditions in industries such as oil and gas, chemical processing, and power generation. They are specifically engineered to withstand extreme temperatures, corrosive media, and high-pressure environments. Their ability to handle chemically reactive and erosive materials makes them suitable for applications where general service butterfly valves fall short.
- Harsh Process Conditions: High performance butterfly valves are ideal for applications involving aggressive or corrosive fluids where conventional butterfly valves may not effectively withstand the conditions.
- High Temperatures and Pressures: When operating in environments with high temperatures and pressures, high performance butterfly valves offer superior performance and reliability.
- Corrosive Media: In industries such as chemical processing, where corrosive media is prevalent, high performance butterfly valves provide essential protection against chemical degradation and erosion.
- Critical Flow Control: For precise throttling and control of flow rates in demanding pipelines, high performance butterfly valves deliver dependable and accurate performance.
- Extended Service Life: When long-term reliability is a priority, high performance butterfly valves offer extended service life and reduced maintenance requirements.
In summary, high performance butterfly valves are the go-to choice for industries where harsh process conditions, aggressive media, and demanding operational parameters necessitate a robust and reliable flow control solution.
Benefits of High Performance Butterfly Valves in Oil and Gas
Enhanced Flow Control and Regulation
High performance butterfly valves are crucial for maintaining precise control over the flow of oil and gas within pipelines. These valves offer superior flow control and regulation, allowing for seamless adjustments in flow rates to suit the operational requirements. Their ability to provide quick and efficient modulation of flow ensures a steady and controlled movement of fluids, essential for the smooth and uninterrupted operation of oil and gas pipelines.
Improved Durability and Longevity
One of the key benefits of high performance butterfly valves in oil and gas applications is their exceptional durability and longevity. Constructed from robust materials and engineered with precision, these valves exhibit resistance to corrosion, wear, and tear, making them ideal for the demanding and harsh environments typically associated with oil and gas operations. Their extended lifespan reduces the frequency of replacements and maintenance, contributing to overall cost savings and operational efficiency.
Energy Efficiency and Reduced Operational Costs
By incorporating high performance butterfly valves into oil and gas pipelines, operators can achieve significant energy efficiency improvements and reduced operational costs. These valves are designed to minimize pressure drop and energy loss, thereby optimizing the overall energy consumption of the system. As a result, the efficient operation of high performance butterfly valves translates into reduced energy expenditures and lower operational costs, making them a valuable asset for oil and gas companies seeking to enhance their operational efficiency and financial performance.
Implementation of High-Performance Butterfly Valves in the Oil and Gas Industry
The implementation of high-performance butterfly valves in the oil and gas industry has proven to be a game-changer, with notable case studies showcasing significant improvements in flow control and operational efficiencies. Companies have documented substantial cost reductions and enhanced safety measures through the adoption of advanced valve technology.
Case Studies for High-Performance Butterfly Valves
Several case studies highlight the impact of high-performance butterfly valves on oil and gas pipelines. In one instance, a major oil corporation reported a 15% decrease in maintenance costs and a 20% improvement in flow control efficiency after implementing these valves in their pipeline networks. Another case study revealed a 25% reduction in downtime due to valve malfunctions, resulting in substantial cost savings and improved operational continuity.
How to Choose the Right Valve for Your Pipeline
Selecting the appropriate valve for oil and gas pipelines is critical to ensure optimal performance and safety. Factors such as pressure ratings, material compatibility, and size requirements should be carefully evaluated. Additionally, the ability of the valve to withstand harsh environmental conditions and corrosive materials is paramount in the selection process. Engaging with experienced valve manufacturers and conducting thorough assessments of pipeline specifications are essential steps in choosing the right valve for a specific application.
Installation and Maintenance Considerations
Proper installation and regular maintenance are crucial for maximizing the performance and longevity of high-performance butterfly valves in oil and gas pipelines. Installation procedures must adhere to industry standards and best practices to guarantee the integrity of the valve’s functionality. In addition, implementing a proactive maintenance schedule, including routine inspections and servicing, is imperative to prevent potential operational disruptions and ensure the continued effectiveness of the valves.
The seamless integration of high-performance butterfly valves into oil and gas operations requires meticulous planning and adherence to industry regulations. As companies continue to prioritize efficiency and safety, the selection, installation, and maintenance of these valves play a pivotal role in optimizing flow control and enhancing overall pipeline performance.
The Impact on Safety and Environmental Compliance
Mitigating Risks in Hazardous Environments
Ensuring safety and environmental compliance in hazardous work environments is crucial for the oil and gas industry. The potential for accidents and environmental harm is significant due to the nature of the operations. Implementing stringent safety measures and compliance protocols is essential to safeguard both the workforce and the environment.
- Regular Risk Assessments: Conduct thorough risk assessments to identify potential hazards and implement measures to mitigate these risks.
- Safety Protocols: Establish and enforce strict safety protocols to minimize the likelihood of accidents and injuries.
- Emergency Preparedness: Develop comprehensive emergency response plans to address potential incidents and minimize their impact.
The Role of High-Performance Butterfly Valves in Emission Reduction
In the oil and gas industry, controlling emissions is a key aspect of environmental compliance. High-performance butterfly valves play a critical role in reducing emissions by providing precise flow control and isolation. These valves enable operators to regulate fluid flow with accuracy, minimizing the release of harmful substances into the environment.
- Precise Flow Control: Butterfly valves offer precise control over fluid flow, allowing operators to optimize processes and minimize emissions.
- Leakage Prevention: The tight shutoff characteristics of butterfly valves help prevent fugitive emissions, contributing to environmental compliance.
- Environmental Stewardship: By reducing emissions and promoting efficient operation, butterfly valves support the industry’s commitment to environmental stewardship.
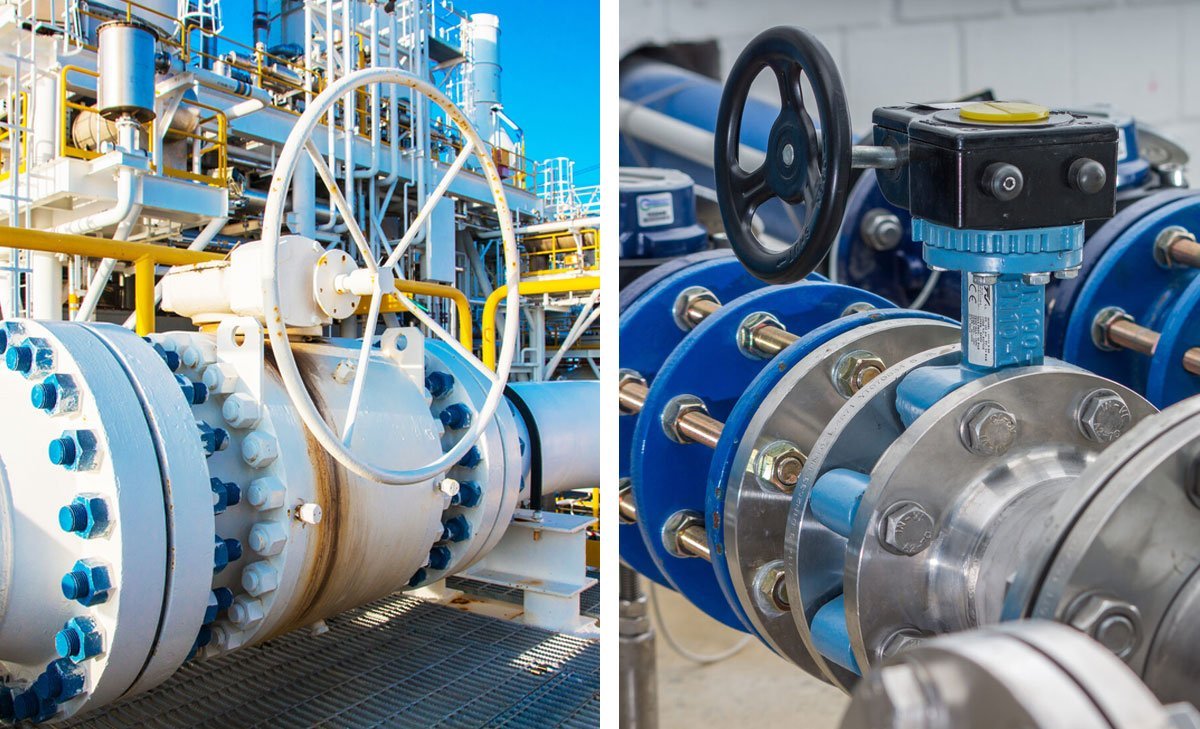
The Future of Flow Control in Pipeline Technology
Ongoing Research and Development in Valve Design
The future of flow control in oil and gas pipelines relies heavily on ongoing research and development in valve design. Engineers and researchers are continually looking for ways to enhance the performance and efficiency of valves used in pipeline systems. This involves studying the behavior of different valve materials under high-pressure and high-temperature conditions, as well as exploring innovative designs to optimize flow control and minimize energy loss.
Cutting-edge materials, such as advanced alloys and high-strength composites, are being investigated for their suitability in valve construction. These materials offer improved resistance to corrosion, erosion, and wear, crucial factors for ensuring the longevity and reliability of valves in harsh pipeline environments. Additionally, the integration of smart technologies into valve design is gaining momentum, enabling real-time monitoring and predictive maintenance to prevent potential issues before they escalate.
Emerging Trends in Butterfly Valve Applications
An emerging trend in pipeline technology is the increasing utilization of high-performance butterfly valves for flow control. These valves offer benefits such as quick and precise throttling, low pressure drop, and tight sealing, making them ideal for applications in oil and gas pipelines. Furthermore, advancements in valve automation and control systems are enhancing the responsiveness and accuracy of butterfly valves, enabling seamless integration with pipeline monitoring and management systems.
Another notable trend is the development of environmentally friendly valve coatings that reduce friction and minimize fluid resistance, contributing to improved energy efficiency in pipeline operations. Furthermore, the integration of data analytics and artificial intelligence into butterfly valve applications is revolutionizing flow control, allowing for proactive optimization of pipeline performance and predictive identification of potential flow disruptions.
In conclusion, the future of flow control in pipeline technology is characterized by continuous innovation in valve design and the widespread adoption of high-performance butterfly valves. These developments are poised to optimize flow management in oil and gas pipelines, offering enhanced operational efficiency, reduced environmental impact, and greater resilience to evolving industry demands.
Conclusion on High-Performance Butterfly Valves
In conclusion, high-performance butterfly valves play a crucial role in improving flow control in oil and gas pipelines. With their innovative design and advanced materials, these valves offer enhanced efficiency, reduced energy loss, and improved system pressure maintenance. Their contribution to sustainability through the reduction of greenhouse gas emissions underscores their significance in modern industrial processes. As technology continues to advance, the future of butterfly valve technology holds the potential for even greater improvements, promising to revolutionize flow control across various industries.