The Pros and Cons of Lug Butterfly Valves in Industrial Applications
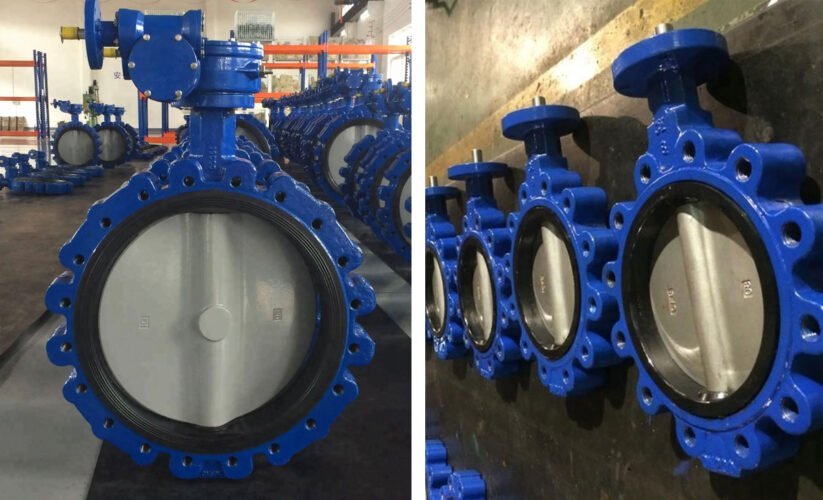
Table of Contents
ToggleUnderstanding Lug Butterfly Valves in Industrial Settings
Lug butterfly valves have become an integral part of various industrial applications, offering benefits as well as posing certain limitations. Understanding the pros and cons of these valves is crucial for making informed decisions regarding their implementation. In this blog post, we will delve into the advantages and drawbacks of lug butterfly valves in industrial settings, shedding light on their functionality and potential impact on operations. Whether you are considering their use or seeking to enhance your knowledge of industrial valves, this exploration will provide valuable insights into the role of lug butterfly valves in industrial applications.
Understanding Lug Butterfly Valves
Basic Design and Operation
A lug butterfly valve is a type of valve designed to regulate the flow of fluids in pipes or hoses. It features metal lugs on the valve’s body, which are utilized to secure the valve between two flanges on a pipe. The primary function of a lug butterfly valve is to utilize a rotating disc that moves perpendicular to the flow of fluid. When the disc aligns parallel to the flow of fluid, the valve opens, allowing fluid passage. Conversely, when the disc is turned perpendicular to the flow of fluid, the valve closes, halting the flow. This design allows for direct proportional control of the valve’s actuation and operating torque based on the valve’s diameter, making it suitable for use in larger pipe sizes.
Typical Uses in Industrial Settings
Lug butterfly valves play a crucial role in fluid control systems across various industries. They are commonly employed in applications where precise regulation of fluid flow and pressure is essential. These include water treatment plants, pharmaceutical manufacturing, food and beverage processing, and petrochemical facilities. The versatility and reliability of lug butterfly valves make them indispensable for isolating sections of piping systems for maintenance or repair, regulating fluid flow rates, and ensuring optimal operational performance. Their straightforward design and effectiveness in fluid control systems have established lug butterfly valves as a preferred choice in industrial settings for managing fluid flow and pressure regulation.
Advantages of Lug Butterfly Valves
Lug butterfly valves offer several advantages that make them a popular choice in various industrial applications.
Cost-Effectiveness
Lug butterfly valves are known for their cost-effectiveness. The design and materials used in these valves make them a more affordable option compared to other types of valves. This cost-effectiveness makes them an attractive choice for budget-conscious projects without compromising on quality and performance.
Space-Saving Design
The space-saving design of lug butterfly valves is another key advantage. Their compact size and lightweight construction make them ideal for installations where space is limited. This design feature allows for more efficient use of available space, making lug butterfly valves suitable for a wide range of industrial settings.
Ease of Installation
One of the notable advantages of lug butterfly valves is their ease of installation. The lug-style design with threaded tapped lugs allows for straightforward bolt connections, simplifying the installation process. This ease of installation can save time and labor costs, making lug butterfly valves a practical choice for various industrial applications.
Versatility in Applications
Lug butterfly valves are highly versatile and can be used in a wide range of applications. Whether it’s in oil and gas, chemical processing, water and wastewater transportation, or HVAC systems, these valves offer flexibility and adaptability. Their compatibility with pneumatic or electric actuation further expands their applicability across different industries.
Maintenance and Durability of Lug Butterfly Valves
When it comes to maintenance and durability, lug butterfly valves excel. Their robust construction and reliable performance reduce the need for frequent maintenance. Additionally, the materials used ensure durability, longevity, and resilience, even in demanding industrial environments. This translates to cost savings and operational efficiency over the long term.
In conclusion, the advantages of lug butterfly valves, including cost-effectiveness, space-saving design, ease of installation, versatility in applications, and maintenance and durability, make them a compelling choice for various industrial settings.
Disadvantages of Lug Butterfly Valves
Lug butterfly valves, while offering various advantages, also present several disadvantages that must be considered for industrial applications.
Limited Pressure Handling
Lug butterfly valves are not suitable for handling high-pressure applications. The design of the valve and the way it is mounted can limit the pressure capacity compared to other types of valves. This limitation can restrict the use of lug butterfly valves in industrial settings where high-pressure fluid handling is required.
Potential for Leakage
One of the main drawbacks of lug butterfly valves is the potential for leakage. The installation of the valve, including the gasket and seal, may be prone to leakage over time. This can lead to inefficiencies and safety concerns in industrial processes, requiring regular maintenance and monitoring to mitigate the risk of leaks.
Wear and Tear Considerations
The continuous operation of lug butterfly valves can lead to wear and tear, especially in applications with frequent opening and closing cycles. The wear on the valve components, such as the disc and seat, can compromise the sealing integrity and performance over time. It’s important for industrial operators to factor in the maintenance and replacement of valve components to address wear and tear issues.
Temperature Constraints of Lug Butterfly Valves
Lug butterfly valves may have limitations in handling extreme temperatures. High temperatures can affect the materials and components of the valve, impacting its performance and longevity. In applications where temperature variations are significant, lug butterfly valves may not be the most suitable choice, requiring careful consideration of temperature constraints.
Considering these disadvantages, industrial users need to weigh the limitations of lug butterfly valves against their specific operational requirements to make informed decisions regarding valve selection and maintenance in fluid handling systems.
Comparison with Other Valve Types
Lug Butterfly Valves vs. Ball Valves
Lug butterfly valves and ball valves are both popular choices in many industrial applications. Ball valves are known for their quick quarter-turn action, making them ideal for situations where fast on/off control is necessary. On the other hand, lug butterfly valves offer a more lightweight and compact design, making them suitable for applications with space constraints. While ball valves provide excellent sealing properties, lug butterfly valves are known for their low-pressure drop and cost-effectiveness. When it comes to maintenance, lug butterfly valves are easier to maintain due to their simple design and fewer components compared to ball valves.
Lug Butterfly Valves vs. Gate Valves
Gate valves are known for their ability to provide a tight seal and minimal fluid resistance, making them suitable for applications where a full flow is required. However, gate valves are more prone to corrosion and can be challenging to maintain. In comparison, lug butterfly valves offer a lighter and more compact alternative, making them easier to install and maintain. Additionally, lug butterfly valves are suitable for applications where space and weight are important considerations.
Performance Lug Butterfly Valves in Extreme Conditions
Lug butterfly valves are designed to perform well in extreme conditions, including high-pressure and high-temperature environments. Their resilient seat design allows them to maintain a tight seal even in harsh operating conditions. In contrast, ball valves may experience limitations in extreme temperatures due to their potential for seat deformation. Gate valves, while known for their robust construction, may face challenges in extreme conditions due to potential stem binding and sealing issues. In extreme conditions, the lightweight and resilient design of lug butterfly valves make them a favorable choice for industrial applications.
Safety Features and Fail-Safe Mechanisms
In industrial applications, safety is of paramount importance when it comes to valve systems. Lug butterfly valves are designed with several safety features and fail-safe mechanisms to ensure smooth operation and prevent potential hazards. Two crucial aspects to consider in this regard are lockout systems and the importance of fail-safe design.
Lockout Systems
Lug butterfly valves are often equipped with lockout systems to prevent unauthorized operation or accidental activation. These systems allow maintenance personnel to securely lock the valve in a closed or open position during service or repair, ensuring the safety of workers and preventing unexpected valve movement that could lead to dangerous situations. By effectively isolating the valve from the process flow, lockout systems contribute to a safer working environment and comply with industry safety regulations.
Fail-Safe Design Importance
The fail-safe design of lug butterfly valves is critical for industrial applications where any system failure could result in significant repercussions. Fail-safe mechanisms are engineered to automatically return the valve to a safe position in the event of power loss or other operational issues. This crucial feature helps prevent potential leaks or process disruptions, safeguarding equipment, personnel, and the surrounding environment. The fail-safe design not only enhances operational reliability but also minimizes the risk of costly downtime and maintenance.
In summary, the inclusion of lockout systems and fail-safe design in lug butterfly valves underscores their commitment to safety and reliability in industrial settings. These features contribute to the overall efficiency of the valve system and provide peace of mind knowing that safety measures are in place to mitigate potential risks.
Selecting the Right Lug Butterfly Valve
When it comes to industrial applications, selecting the right lug butterfly valve dimensions is a critical task that requires careful consideration of several key factors. From assessing the application requirements to ensuring material compatibility, and evaluating the size and pressure ratings, each aspect plays a significant role in determining the effectiveness and efficiency of the valve within the system.
Assessing the Application Requirements
Understanding the specific needs of your project is paramount when selecting lug butterfly valve dimensions. Factors such as the flow rate, temperature range, and the type of fluid being handled must be thoroughly evaluated. For instance, a system dealing with corrosive substances would require a valve made from a material that offers excellent corrosion resistance, such as stainless steel. Additionally, the environmental conditions under which the valve will operate should be taken into account to ensure optimal performance and longevity.
Material Compatibility
The material from which the lug butterfly valve is constructed is crucial in determining its suitability for the intended application. Different materials exhibit varying properties that make them suitable for specific environments and fluids. For example, if the system handles abrasive media, a valve with a durable and wear-resistant material, such as high-performance polymers or specially coated alloys, may be required. It’s essential to consider the potential chemical reactions between the valve material and the fluids it will come into contact with to prevent degradation and ensure the longevity of the valve.
Size and Pressure Ratings of Lug Butterfly Valves
The size of the valve must align with the dimensions of the pipe system in which it will be installed to ensure a proper fit and functionality. Additionally, evaluating the pressure ratings of the valve is crucial, as it determines the maximum pressure the valve can withstand without compromising its integrity. Ensuring that the selected valve’s pressure rating exceeds the maximum pressure expected within the system is essential to prevent failure and maintain operational safety.
By carefully considering these factors and selecting the right lug butterfly valve dimensions based on the specific requirements of your industrial application, you can ensure enhanced performance, longevity, and operational efficiency within your system.
Installation and Maintenance Best Practices
Proper Installation Procedures of Lug Butterfly Valves
When installing lug butterfly valves in industrial applications, it is crucial to follow proper installation procedures to ensure optimal performance and longevity. Start by thoroughly inspecting the valve and ensuring that it is free from any damage or defects. Proper alignment and support are essential to prevent stress on the valve and ensure a tight seal. Additionally, using the correct tools and following manufacturer guidelines for torque specifications is critical to avoid issues such as leakage or operational inefficiencies.
Routine Maintenance Tips
Routine maintenance is essential for the ongoing functionality of lug butterfly valves. This includes regular inspection of the valve body, disc, and stem for signs of wear, corrosion, or buildup. Lubrication of the valve components to minimize friction and ensure smooth operation is also important. Additionally, checking and adjusting the valve packing to prevent leaks is vital for maintaining optimal performance. Keeping detailed maintenance records can aid in identifying any patterns of wear or issues that may require attention.
Common Mistakes to Avoid
Avoiding common mistakes in the installation and maintenance of lug butterfly valves can help prevent costly repairs and downtime. One common mistake is over-tightening the valve, which can lead to distortion and operational issues. Neglecting routine maintenance and inspections can also result in unexpected valve failure. Using the wrong type of lubricant or not applying it correctly can cause premature wear and reduced functionality. Lastly, failing to follow manufacturer recommendations for installation and maintenance can compromise the overall performance and lifespan of the valve.
Conclusion
In conclusion, lug butterfly valves offer advantages such as easy installation, minimal maintenance, and cost-effectiveness. They are ideal for applications that require bi-directional shutoff and dead-end service. However, they also have limitations, including potential difficulty in repairing or replacing the valve without disrupting the entire pipeline. It’s important for industrial professionals to carefully consider these pros and cons when determining the suitability of lug butterfly valves for their specific applications.