Unraveling the Anatomy of a Needle Valve
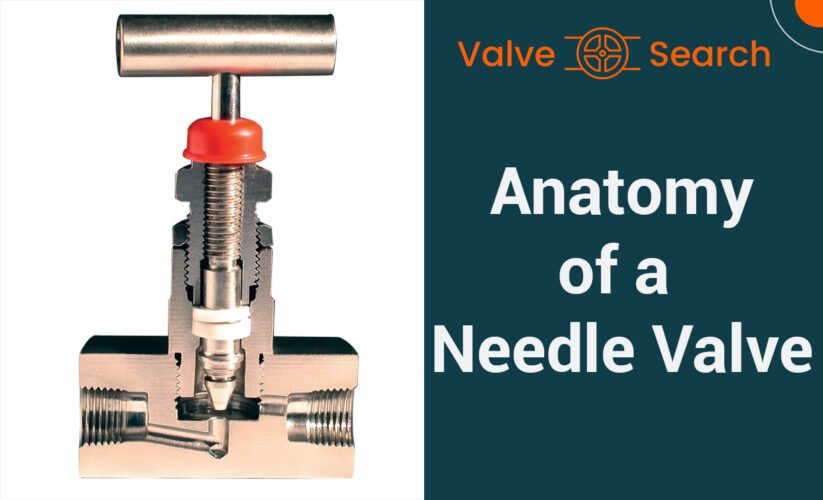
Table of Contents
ToggleIntroduction
If you’ve ever taken a closer look at the components that make up complex machinery or plumbing systems, you may have come across a small, often overlooked component known as the needle valve. This simple yet intricately designed part plays a critical role in regulating the flow of fluids in systems ranging from your car engine to industrial processing plants. This article seeks to delve into the intricate anatomy of the needle valve, explaining its design, function, and role in various industries.
Inside the Complex Structure of a Needle Valve
While a needle valve may appear to be a straightforward component, it boasts a complex structure. Its design intricacies are found in the way its different elements interrelate to provide precise fluid flow control. Central to the needle valve’s structure is a slim, rod-like piece called the plunger. This critical component adjusts fluid flow within the system.
The plunger is linked to the handle of the valve by the valve stem, enabling the user to manipulate the plunger’s position. Another vital part of a needle valve is the valve seat. This component is the contact point for the plunger when the valve is in the closed position, ensuring a tight seal is formed to halt fluid flow. Thus, the complexity of the needle valve is hidden within the interplay of these essential components.
How does a Needle Valve Work?
The operation of a needle valve is simple yet intriguing. When the handle of the valve is rotated, it instigates a movement in the plunger. Should the plunger be driven downward, it settles into the valve seat, completely obstructing the path of the fluid.
A counter-movement is initiated when the handle is rotated in the opposite direction, lifting the plunger and consequently creating a passage for the fluid to pass through. The degree of rotation imparted to the handle is directly proportional to the size of the opening and, therefore, governs the rate at which the fluid flows. The delicate equilibrium of these movements permits the needle valve to perform its crucial role in systems requiring precise fluid flow control.
Understanding the Core Components of a Needle Valve
The core components of a needle valve, the plunger and the valve stem, are integral to its operation. The plunger’s architecture enables it to execute two primary functions: establishing an extremely secure seal when the valve is closed and providing precise regulation of fluid flow when the valve is open.
The valve stem, conversely, serves as the crucial conduit between the plunger and the manual or automated input from an operator. Its role is to effectively communicate this input to the plunger, ultimately enabling the operator to effectively manage the flow rate within a system. These components’ symbiotic relationship, along with their individual attributes, are fundamental to the proper functioning of a needle valve.
The Role of the Needle Valve in Flow Control
In various systems, needle valves are more than just a component – they are a critical control element. With their unique ability to precisely regulate fluid flow, they maintain an essential role in environments where a specific flow rate must be upheld. For instance, in the domain of automotive engineering, the fuel injection process relies heavily on the meticulous control provided by needle valves.
Without their precision, the balance of fuel to the engine could be disrupted, negatively impacting performance. Equally, in water treatment plants, where the exact dosing of chemicals is pivotal to the process, the needle valve emerges as a trusted ally. Its design and operation ensure the correct amount of chemicals are introduced, safeguarding both efficiency and safety. Whether in the vehicle in your driveway or the unseen infrastructure that purifies your water, the needle valve’s role in flow control is paramount.
In processes demanding meticulous control of fluid flow, like in chemical or pharmaceutical manufacturing, minute shifts in pressure or temperature can dramatically impact product quality and yield. Needle valves prove integral in these situations, providing reliable and consistent flow regulation.
What does a Needle Valve do?
The primary function of a needle valve is to regulate the flow of fluids or gases within a system. It does this by making fine adjustments to a narrow passageway, hence the name ‘needle’. As you turn the valve’s handle, it moves the plunger up or down, narrowing or widening the pathway that the fluid travels through. This modulation allows for exceptional control over the fluid’s flow rate, ensuring a precise measurement of the fluid or gas that’s being transported through a system.
Despite its modest size, the needle valve’s impact is significant. In circumstances requiring meticulous flow control, like fuel injection in a car or chemical dosing in a water treatment plant, it’s the needle valve that ensures accuracy and consistency. Its ability to provide a secure seal when closed also means it’s trusted to prevent fluid or gas leakage, contributing to the safety and efficiency of the system it operates within.
In a broader sense, a flow control needle valve serves as a vital part of managing the overall performance of an entire system. It contributes to the efficiency, accuracy, and safety of many processes in diverse industries. Whether it’s maintaining the correct fuel-air mixture in a car engine, regulating the flow of gas in pipelines, or controlling chemical dosing in water treatment facilities, the needle valve is essential in maintaining operational standards and achieving desired results. So while a needle valve may appear unassuming, its role is pivotal, and its functionality is multifaceted and dynamic.
Plunger Valves
Diving deeper into the types of needle valves, we come across the plunger valve. Closely resembling the anatomy of a standard needle valve, the plunger valve differs slightly in design and function.
The primary distinction lies in the shape of the valve’s central element, known as the plunger. Unlike the needle valve’s rod-like plunger, the plunger in a plunger valve typically has a broader, cylindrical shape. This subtle variation in design impacts the valve’s functionality, allowing for a quicker and more robust fluid flow adjustment.
While a needle valve excels in delivering precise flow control, a plunger valve is often favored in applications requiring swift flow interruption or full opening. Despite their differences, both the plunger valve and the traditional needle valve share the common objective of regulating fluid flow, showcasing the versatile application of the plunger mechanism within various valve types.
The Use of Needle Valves in Various Industries
From the automobile sector to oil and gas, the functionality and utility of needle valves span across multiple industries. Their role in automotive fuel injection systems is critical; they regulate the fuel flow, ensuring the engine operates efficiently. Their presence is equally significant in the oil and gas sector, where they meticulously manage oil and gas flow within pipelines, reducing waste and maximizing productivity.
In the water treatment realm, they take on a crucial task of precisely controlling the quantity of chemicals administered in the water. Their exceptional control enables them to dispense exact doses, upholding safety and efficiency in this critical process. Across these varied industries, the needle valve consistently proves its worth, offering precise control, enhancing safety and boosting overall operational efficiency.
Challenges and Solutions in Needle Valve Design
In the quest to develop reliable and efficient needle valves, designers and manufacturers face a couple of notable obstacles. One of the primary challenges is the creation of a seal that is both secure and resilient when the valve is in a closed position. Another significant hurdle is the natural wear and tear that arises due to continuous usage, which can potentially compromise the valve’s effectiveness.
Recognizing these issues, the industry has devised several strategies to surmount these challenges. For instance, the selection of robust materials such as stainless steel or brass for the construction of needle valves ensures they can withstand regular usage without succumbing to wear and tear. Additionally, these materials offer superior resistance to corrosion, enhancing the longevity of the needle valve.
Further, to guarantee a secure seal, manufacturers employ advanced methods such as thread-locking. This technique helps to preserve the plunger’s position once it has been adjusted, maintaining the desired flow rate and eliminating potential leaks. Through the integration of such practices, the needle valve design effectively addresses the prevalent challenges, thereby optimizing the valve’s performance and durability.
How have advancements in technology impacted needle valve design over time?
Technological advancements have dramatically impacted the design of needle valves, optimizing their efficiency and precision. Initially, needle valves were manually adjusted, which required constant monitoring and could be susceptible to human error.
Today, automation technology has revolutionized valve’s design, allowing for automated adjustment of the plunger valve position. This development ensures a more precise, consistent, and efficient regulation of fluid flow. Advancements in materials science have also played a significant role. The introduction of more durable, corrosion-resistant materials has greatly enhanced the lifespan and performance of needle valves.
Additionally, the integration of digital sensors into the needle valve’s design allows for real-time monitoring and adjustments, leading to improved accuracy in flow control. This evolution reflects the impact of technological progress on even the smallest, seemingly simple components, underscoring the profound influence of innovation on every aspect of industry operations.
The Future of Needle Valve Technology
The horizon of needle valve technology is evolving in tandem with advancements in automation and digital intelligence. The coming generation of these valves will likely incorporate real-time data from integrated sensors, enabling them to self-regulate the flow rate according to the system’s immediate needs.
This intelligent functionality will raise the bar for both the safety and efficiency of systems that employ needle valves. The automation will reduce the need for manual adjustments, while real-time data analysis will ensure optimal flow regulation. This marks a significant stride forward in the valve technology space, signaling a future where needle valves are not just components, but integral, intelligent elements of a system.
The forthcoming developments in needle valve technology are set to further emphasize the valve’s importance and versatility in various industries, reinforcing its indispensable role in precise fluid control. The evolution of needle valve technology, therefore, holds promising potential for enhancing system performance and operational efficiency.
Conclusion
In the realm of fluid control, the needle valve emerges as an understated yet critical component. With its sophisticated design and precision in regulating flow, it plays a pivotal role across diverse industries, from automotive to water treatment. The interplay of its core components, including the plunger and the valve stem, give it the ability to provide an exceptionally secure seal and precise flow regulation.
As the future unfolds, the needle valve is set to harness the power of automation and real-time data analysis, further boosting its efficiency and versatility. Regardless of its size or the simplicity of its appearance, the needle valve’s impact is unmistakable and indispensable. It serves as a testament to the incredible engineering ingenuity that goes into even the smallest, often overlooked parts of a system, and reminds us that every piece, no matter how small, plays a significant role in the greater whole.